Cement grinding system and method
A technology of cement powder and dust collection system, which is applied in chemical instruments and methods, solid separation, filter and sieve, etc. It can solve the problems of low grinding efficiency, high operating cost, and large installed power, so as to prevent over-grinding and improve energy utilization. The effect of high efficiency and low installed power
- Summary
- Abstract
- Description
- Claims
- Application Information
AI Technical Summary
Problems solved by technology
Method used
Image
Examples
Embodiment 1
[0040] A cement grinding system such as figure 1 As shown, it includes a vibrating screen 03, a steady flow and constant weight bin 04, a roller press 05, a ball mill 06, a double-rotor powder separator 11, a stirring mill 15 and a dust collection system. The vibrating screen 03 includes an outlet on the sieve and a screen The lower outlet, wherein the outlet under the sieve is connected to the feed inlet of the ball mill 06, the outlet on the sieve is connected to the feed inlet of the steady flow constant weight bin 04, and the outlet of the steady flow constant weight bin 04 is connected to the feed of the roller press 05 The discharge port of the roller press 05 is connected through the hoist 02 and returns to the vibrating screen 03; the double-rotor powder separator 11 includes a bottom discharge port, a waist discharge port and a top air discharge port, wherein the top discharge port The tuyere is connected to the finished product collection system, the waist discharge ...
PUM
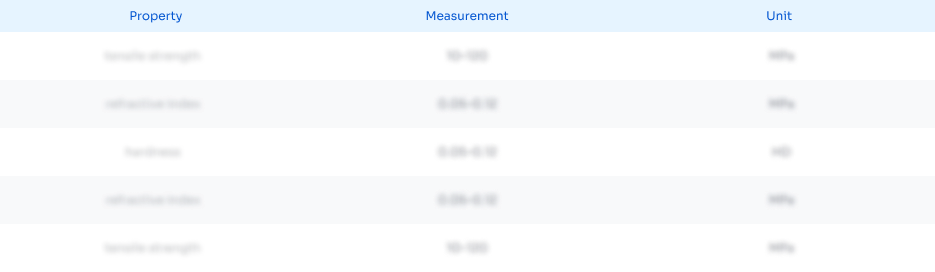
Abstract
Description
Claims
Application Information

- R&D
- Intellectual Property
- Life Sciences
- Materials
- Tech Scout
- Unparalleled Data Quality
- Higher Quality Content
- 60% Fewer Hallucinations
Browse by: Latest US Patents, China's latest patents, Technical Efficacy Thesaurus, Application Domain, Technology Topic, Popular Technical Reports.
© 2025 PatSnap. All rights reserved.Legal|Privacy policy|Modern Slavery Act Transparency Statement|Sitemap|About US| Contact US: help@patsnap.com