Power plant flue gas treatment system
A flue gas treatment system and flue gas technology are applied in the treatment of combustion products, combustion methods, indirect carbon dioxide emission reduction, etc., which can solve the problem of low temperature corrosion of air preheaters and blockage of ammonium hydrogen sulfate and high leakage risks of water-based heat exchangers. , high maintenance and operating costs, to achieve the effect of eliminating corrosion risks, facilitating on-site layout, and reducing maintenance and operating costs
- Summary
- Abstract
- Description
- Claims
- Application Information
AI Technical Summary
Problems solved by technology
Method used
Image
Examples
Embodiment 1
[0019] A power plant flue gas treatment system, such as figure 1 As shown, it includes a flue path mainly composed of a boiler 1, a rotary air preheater 2, a flue gas heater 4, an induced draft fan 5, a desulfurization tower 6 and a chimney 8, and the flue gas heater 4 adopts As the cooling medium, the air is introduced into the flue gas heater 4 and exchanges heat with the flue gas flowing through the flue gas heater 4, and the medium-temperature wind obtained from the heat exchange is introduced into the rotary air preheater 2, and the medium-temperature wind and the flow The flue gas from the rotary air preheater 2 performs heat exchange, the first part of the hot air obtained from the heat exchange is introduced into the boiler 1 as a heat source, and the second part of the hot air obtained from the heat exchange is cooled by heat exchange and used as a part of the flue gas heater 4 cold medium.
[0020] Among them, the air volume used for the flue gas heater 4 is 10%-20%...
Embodiment 2
[0028] A power plant flue gas treatment system, such as figure 2 As shown, it includes a flue path mainly composed of a boiler 1, a rotary air preheater 2, a flue gas heater 4, an induced draft fan 5, a desulfurization tower 6 and a chimney 8, and the flue gas heater 4 adopts As the cooling medium, the air is introduced into the flue gas heater 4 and exchanges heat with the flue gas flowing through the flue gas heater 4, and the medium-temperature wind obtained from the heat exchange is introduced into the rotary air preheater 2, and the medium-temperature wind and the flow The flue gas from the rotary air preheater 2 performs heat exchange, the first part of the hot air obtained from the heat exchange is introduced into the boiler 1 as a heat source, and the second part of the hot air obtained from the heat exchange is cooled by heat exchange and used as a part of the flue gas heater 4 cold medium.
[0029] Among them, the air volume used for the flue gas heater 4 is 10%-20...
PUM
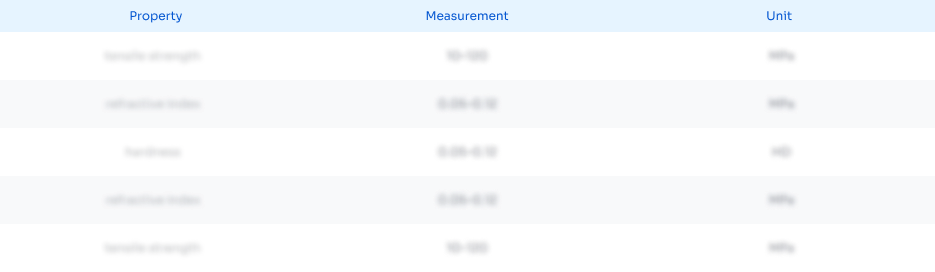
Abstract
Description
Claims
Application Information

- R&D
- Intellectual Property
- Life Sciences
- Materials
- Tech Scout
- Unparalleled Data Quality
- Higher Quality Content
- 60% Fewer Hallucinations
Browse by: Latest US Patents, China's latest patents, Technical Efficacy Thesaurus, Application Domain, Technology Topic, Popular Technical Reports.
© 2025 PatSnap. All rights reserved.Legal|Privacy policy|Modern Slavery Act Transparency Statement|Sitemap|About US| Contact US: help@patsnap.com