Novel glass fiber reinforced plastic lining concrete combined pipe
A technology that is lined with concrete and glass fiber reinforced plastics, applied in the field of pipelines, can solve problems such as heat dissipation, cracked pipelines, and antifreeze problems
- Summary
- Abstract
- Description
- Claims
- Application Information
AI Technical Summary
Problems solved by technology
Method used
Image
Examples
Embodiment
[0021] like figure 1 As shown in the figure, the novel FRP lined concrete composite pipe includes a FRP inner lining layer 1, an elastic interface layer 2, a functional layer 3 and a concrete layer 4 sequentially arranged from the inside to the outside.
[0022] The elastic interface layer 2 is a material with elasticity and a relatively large friction coefficient, such as resin or the like. The frictional force of the elastic interface layer 2 is relatively large, which prevents displacement of the FRP inner lining layer 1 , the functional layer 3 and the concrete layer 4 .
[0023] Further, one end of the FRP lining pipe is provided with a socket 5 , the other end of the FRP lining pipe is provided with a socket 6 , and a groove mounting sealing ring 7 is provided on the socket 5 . The connection of the two combined pipes is realized by a traditional plug-in method. Since it is the prior art, this embodiment will not describe in detail.
[0024] It is worth emphasizing tha...
PUM
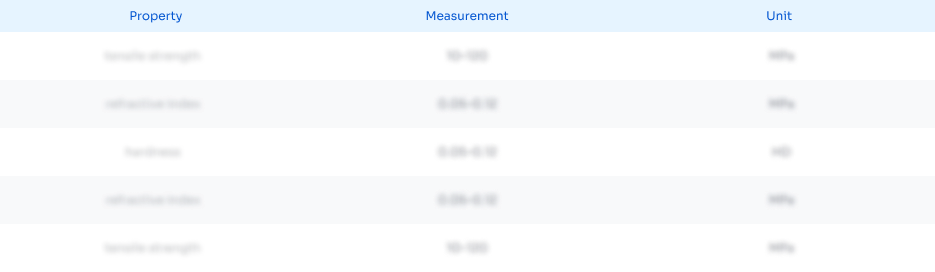
Abstract
Description
Claims
Application Information

- R&D Engineer
- R&D Manager
- IP Professional
- Industry Leading Data Capabilities
- Powerful AI technology
- Patent DNA Extraction
Browse by: Latest US Patents, China's latest patents, Technical Efficacy Thesaurus, Application Domain, Technology Topic, Popular Technical Reports.
© 2024 PatSnap. All rights reserved.Legal|Privacy policy|Modern Slavery Act Transparency Statement|Sitemap|About US| Contact US: help@patsnap.com