Modified lignin, preparation method and application of modified lignin in toughening flame-retardant composite material
A technology of flame-retardant composite materials and lignin, which is applied in the field of preparation of toughened flame-retardant composite materials, can solve problems such as poor dispersion, degradation of polyester polymer materials, and polymer embrittlement, and achieve the effect of improving toughness
- Summary
- Abstract
- Description
- Claims
- Application Information
AI Technical Summary
Problems solved by technology
Method used
Image
Examples
Embodiment 1
[0026] A preparation method of modified lignin, the steps are:
[0027] (1) Add melamine and formaldehyde with a mass ratio of 1:0.15 to water, and stir for 2 hours at 60°C;
[0028] (2) Alkaline lignin, formaldehyde and phytic acid are gradually added to the solution obtained in step (1) in a mass ratio of 0.5:0.25:0.5:1 to melamine, react at 90° C. for 5 hours, and filter and dry to obtain Modified lignin, denoted as LMP;
Embodiment 2
[0030] A preparation method of modified lignin, the steps are:
[0031] (1) Add melamine and formaldehyde with a mass ratio of 1:0.25 to water, and stir for 0.5h at 80°C;
[0032] (2) adding alkaline lignin, formaldehyde and phytic acid to melamine in a mass ratio of 1:0.5:1:1 into the solution obtained in step (1) step by step, reacting at 90° C. for 5 hours, and filtering and drying to obtain Modified lignin, denoted as LMP';
[0033] According to the formula and process listed in Table 1, the products obtained in Examples 1 and 2 were blended and granulated to obtain the masterbatches of the modified lignin toughened and flame-retardant composite materials of Examples 5-11 and the corresponding Comparative Examples 1-4.
[0034] Table I
[0035]
[0036]
PUM
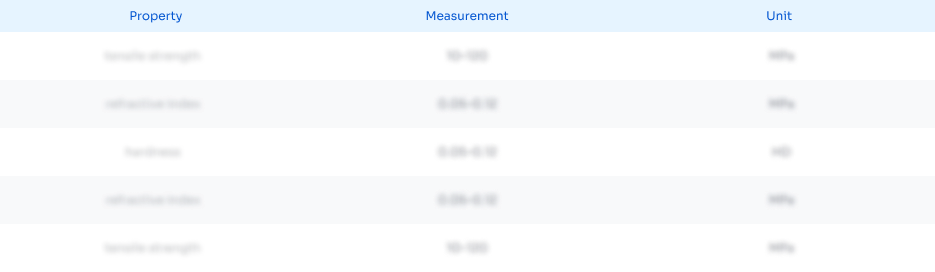
Abstract
Description
Claims
Application Information

- Generate Ideas
- Intellectual Property
- Life Sciences
- Materials
- Tech Scout
- Unparalleled Data Quality
- Higher Quality Content
- 60% Fewer Hallucinations
Browse by: Latest US Patents, China's latest patents, Technical Efficacy Thesaurus, Application Domain, Technology Topic, Popular Technical Reports.
© 2025 PatSnap. All rights reserved.Legal|Privacy policy|Modern Slavery Act Transparency Statement|Sitemap|About US| Contact US: help@patsnap.com