Waste alkaline residue recycling method and alkaline residue self-repairing cement-based material prepared by same
A cement-based material and self-repairing technology, applied in the field of building materials, can solve problems such as pollution in the surrounding sea area, and achieve the effects of high survival rate, high alkali resistance, and high survival rate.
- Summary
- Abstract
- Description
- Claims
- Application Information
AI Technical Summary
Problems solved by technology
Method used
Examples
Embodiment 1
[0026] This embodiment provides a method for reusing waste alkali slag. First prepare the raw materials according to the following proportioning ratio: 1 part of ordinary Portland cement P.O. Mix it with cement and stir it evenly to obtain a dry material mixture, then add the pasteurized spore solution, and stir it evenly to obtain a cement slurry-experimental group B1 (alkali slag self-repairing cement-based material). After testing, the number of Pasteurella per milliliter of cement slurry was 10 9 indivual.
[0027] Make the control group mortar N1, use the same cement and water-cement ratio, and use ordinary fine sand with similar strength as the substitute of alkali slag to make the control group mortar. The specific composition of N1 is 1 part of ordinary Portland cement 42.5 cement, 0.35 part of water, and 0.35 part of fine sand.
[0028] The two groups were put into the mold and vibrated 60 times respectively, and were put into the standard curing box for curing for ...
Embodiment 2
[0032] This embodiment provides a method for reusing waste alkali slag. First, the raw materials are prepared according to the following proportioning ratio: 1 part of ordinary Portland cement P.O. Mix it with cement and stir evenly to obtain a dry material mixture, then add pasteurized spore solution, and stir evenly to obtain cement slurry-experimental group B2 (alkali slag self-repairing cement-based material). After testing, the number of Pasteurella per milliliter of cement slurry was 10 8 indivual.
[0033] Make the mortar N2 of the control group, use the same cement and water-cement ratio, and use ordinary fine sand with similar strength as the substitute of alkali slag to make the mortar of the control group. The specific composition of N2 is 1 part of ordinary Portland cement 42.5 cement, 0.40 part of water, and 0.35 part of fine sand.
[0034] The two groups were put into the mold and vibrated 60 times respectively, and were put into the standard curing box for cur...
Embodiment 3
[0038] This embodiment provides a method for reusing waste alkali slag. First, the raw materials are prepared according to the following proportioning ratio: 1 part of ordinary Portland cement P.O. Mix with cement and stir evenly to obtain a dry material mixture, then add the pasteurized spore solution, and stir evenly to obtain cement slurry-experimental group B3 (alkali slag self-repairing cement-based material). After testing, the number of Pasteurella per milliliter of cement slurry was 10 7 indivual.
[0039] Make the mortar N3 of the control group, use the same cement and water-cement ratio, and use ordinary fine sand with similar strength as the substitute of alkali slag to make the mortar of the control group. The specific components of N3 are 1 part of ordinary Portland cement 42.5 cement, 0.40 part of water, and 0.40 part of fine sand. Stir evenly into the mold and vibrate 60 times.
[0040]The two groups were put into the mold and vibrated 60 times respectively, a...
PUM
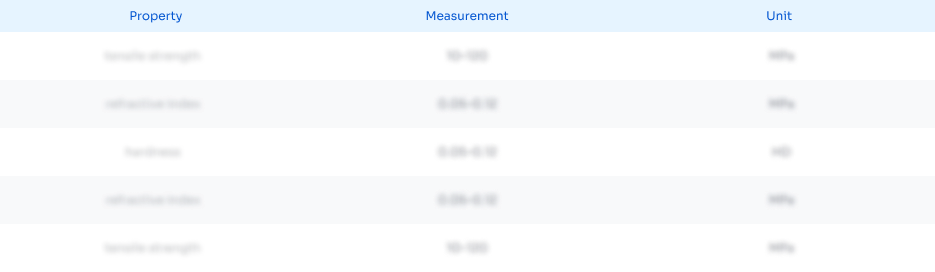
Abstract
Description
Claims
Application Information

- R&D Engineer
- R&D Manager
- IP Professional
- Industry Leading Data Capabilities
- Powerful AI technology
- Patent DNA Extraction
Browse by: Latest US Patents, China's latest patents, Technical Efficacy Thesaurus, Application Domain, Technology Topic, Popular Technical Reports.
© 2024 PatSnap. All rights reserved.Legal|Privacy policy|Modern Slavery Act Transparency Statement|Sitemap|About US| Contact US: help@patsnap.com