Welding method of WTi target material assembly
A welding method and target material technology, applied in welding equipment, welding/welding/cutting items, non-electric welding equipment, etc., can solve problems such as short service life, unsatisfactory sputtering effect, and easy cracks in WTi
- Summary
- Abstract
- Description
- Claims
- Application Information
AI Technical Summary
Problems solved by technology
Method used
Image
Examples
Embodiment 1
[0037] This embodiment provides a welding method for a WTi target assembly. The welding method includes: assembling a WTi target 2, an aluminum back plate 3 and a cover plate 1, and then putting them into a sheath for degassing treatment and welding;
[0038] Wherein, the welding surface of the WTi target 2 is provided with grooves; the welding surface of the aluminum back plate 3 is subjected to alkali treatment; the assembly is that the aluminum back plate 3 and the cover plate 1 are symmetrically assembled with the WTi target 2 as the center, Such as figure 1 As shown; the width of the groove is 3mm; the vertical depth of the groove is 1mm; the distance between the grooves is 4mm; the groove is a rectangular groove; Treatment; the alkali solution is sodium hydroxide solution; the concentration of the alkali solution is 10mol / L; the time of the alkali treatment is 15min; the temperature of the degassing treatment is 400°C; the heat preservation of the degassing treatment T...
Embodiment 2
[0041] This embodiment provides a welding method for a WTi target assembly. The welding method includes: assembling a WTi target, an aluminum back plate and a cover plate, and then placing them in a sheath for degassing and welding in sequence;
[0042] Wherein, the welding surface of the WTi target is provided with grooves; the welding surface of the aluminum back plate is subjected to alkali treatment; the assembly is that the aluminum back plate and the cover plate are assembled symmetrically with the WTi target as the center; the width of the groove 2mm; the vertical depth of the groove is 1.5mm; the distance between the grooves is 5mm; the groove is an inverted triangular groove; It is potassium hydroxide solution; the concentration of the alkali solution is 6mol / L; the time of the alkali treatment is 25min; the temperature of the degassing treatment is 310°C; the holding time of the degassing treatment is 3h; The final vacuum degree of degassing treatment is 4×10 -3 Pa;...
Embodiment 3
[0045] This embodiment provides a welding method for a WTi target assembly. The welding method includes: assembling a WTi target, an aluminum back plate and a cover plate, and then placing them in a sheath for degassing and welding in sequence;
[0046] Wherein, the welding surface of the WTi target is provided with grooves; the welding surface of the aluminum back plate is subjected to alkali treatment; the assembly is that the aluminum back plate and the cover plate are assembled symmetrically with the WTi target as the center; the width of the groove The vertical depth of the groove is 0.5mm; the distance between the grooves is 3mm; the groove is an inverted trapezoidal groove; the alkali treatment is to use alkali solution to process the welding surface of the aluminum back plate; It is sodium hydroxide solution; the concentration of the alkali solution is 12mol / L; the time of the alkali treatment is 10min; the temperature of the degassing treatment is 477°C; the holding ti...
PUM
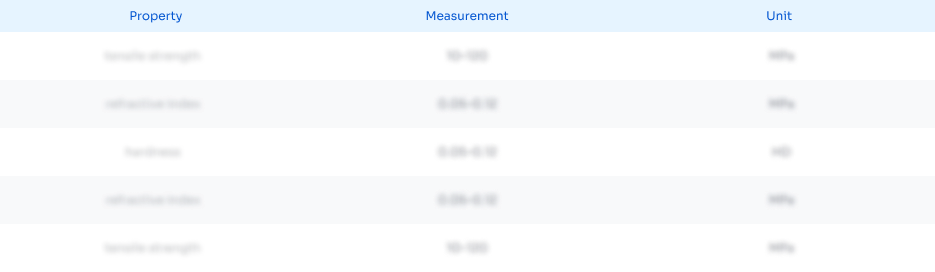
Abstract
Description
Claims
Application Information

- R&D
- Intellectual Property
- Life Sciences
- Materials
- Tech Scout
- Unparalleled Data Quality
- Higher Quality Content
- 60% Fewer Hallucinations
Browse by: Latest US Patents, China's latest patents, Technical Efficacy Thesaurus, Application Domain, Technology Topic, Popular Technical Reports.
© 2025 PatSnap. All rights reserved.Legal|Privacy policy|Modern Slavery Act Transparency Statement|Sitemap|About US| Contact US: help@patsnap.com