Anode alloy material for magnesium air battery, preparation method thereof and battery
An anode alloy and air battery technology, applied in the field of materials, can solve the problems of large magnesium, strong hydrogen evolution, self-corrosion, and hindering the dissolution of magnesium anodes
- Summary
- Abstract
- Description
- Claims
- Application Information
AI Technical Summary
Problems solved by technology
Method used
Image
Examples
preparation example Construction
[0028] The preparation method of the anode alloy material for the magnesium-air battery includes:
[0029] The cast slab is subjected to solution treatment, rolling, and annealing, and the content of each element component contained in the cast slab matches the element component content of the anode alloy material to be prepared.
[0030] Specifically:
[0031] S1, preparation of cast slab
[0032] Prepare the material according to the content requirements of each element component in the anode alloy material. Then, the pure magnesium ingot is melted and then pure aluminum, pure bismuth, pure calcium, Mg-Ca alloy and Mg-Ce alloy are added to it, and then refined, stirred, slag-removed, and placed to obtain a casting billet.
[0033] Preferably, Mg-Ca alloy and Mg-Ce alloy are respectively selected as Mg-20Ca master alloy and Mg-25Ce master alloy.
[0034] S2, solution treatment
[0035] The slab is obtained by solution treatment of the cast slab in a two-stage solution treatment method. ...
Embodiment 1
[0050] Material preparation: According to the mass percentage content of each element in the alloy:
[0051] 7.5% Al, 5.6% Ca, 3.4% Bi, 3.5% Ce, the limiting elements are Fe≤0.01%, Cu≤0.01%, Ni≤0.01%, and the rest are Mg for material preparation.
[0052] First, the pure magnesium ingot with a magnesium content of 99.99% is heated and melted. Under the protection of the flux, the temperature is raised to 680~760℃ for smelting. According to the composition ratio, pure aluminum, pure bismuth and Mg-20Ca and Mg-25Ce master alloys are added successively. Refining, stirring, removing slag, pouring after standing to obtain a magnesium alloy anode material cast blank for air battery.
[0053] Then, the cast slab is subjected to two-stage solution treatment, the low-temperature solution temperature is 350℃, and the holding time is 4h; the high-temperature solution temperature is 480℃, and the holding time is 9h; the slab after the two-stage solution treatment is removed from the surface Aft...
Embodiment 2
[0055] Material preparation: According to the mass percentage content of each element in the alloy:
[0056] 1.5% Al, 6.5% Ca, 0.2% Bi, 4.0% Ce, restricted elements Fe≤0.01%, Cu≤0.01%, Ni≤0.01%, and the rest are Mg for material preparation.
[0057] First, the pure magnesium ingot with a magnesium content of 99.99% is heated and melted. Under the protection of the flux, the temperature is raised to 680°C for smelting. According to the composition ratio, pure aluminum, pure bismuth and Mg-20Ca and Mg-25Ce master alloys are added successively. Stirring, removing slag, pouring after standing to obtain a magnesium alloy anode material cast blank for air battery.
[0058] Then, the cast slab is subjected to two-stage solution treatment, the low-temperature solution temperature is 300℃, and the holding time is 2h; the high-temperature solution temperature is 400℃, and the holding time is 8h; the slab after the two-stage solution treatment is removed from the surface After the oxide layer,...
PUM
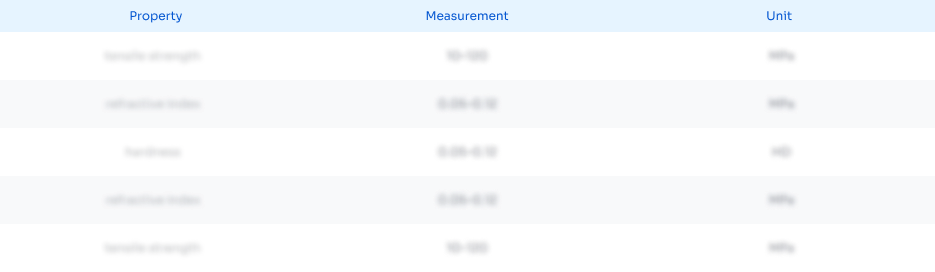
Abstract
Description
Claims
Application Information

- Generate Ideas
- Intellectual Property
- Life Sciences
- Materials
- Tech Scout
- Unparalleled Data Quality
- Higher Quality Content
- 60% Fewer Hallucinations
Browse by: Latest US Patents, China's latest patents, Technical Efficacy Thesaurus, Application Domain, Technology Topic, Popular Technical Reports.
© 2025 PatSnap. All rights reserved.Legal|Privacy policy|Modern Slavery Act Transparency Statement|Sitemap|About US| Contact US: help@patsnap.com