Coal fired boiler novel combustion system
A combustion system and coal-fired boiler technology, applied in combustion methods, combustion equipment, combustion technology mitigation and other directions, can solve the problems of insufficient boiler combustion, waste of resources, large power consumption of fans, etc., to save energy, reduce emissions, ensure full burn effect
- Summary
- Abstract
- Description
- Claims
- Application Information
AI Technical Summary
Problems solved by technology
Method used
Image
Examples
Embodiment 1
[0035] Example 1, taking a 40T coal-fired boiler as an example, when the boiler produces the same amount of water vapor, the comparison results of the relevant parameters of the new combustion system of the coal-fired boiler and the relevant parameters of the existing combustion system are shown in Table 1 :
[0036] Table 1
[0037]
[0038]
[0039] Change the blower 7 from two or more to one, the power of the blower 7 from 110kW to 22kW, and the flow of the blower 7 from 47000 to 83000m 3 / h is changed to 7700~9500m 3 / h; the pressure of the blower 7 is changed from the original low pressure 4200~2900Kpa to the high pressure 7300~6600Kpa.
[0040] The motor power of the induced draft fan 9 is changed from the original 335KW to 37KW; the flow rate of the induced draft fan 9 is changed from the original 73000 to 174000m 3 / h is changed to 13000~17000m 3 / h. The oxygen content in the combustion zone of the boiler 1 is increased by using water vapor with oxygen molec...
Embodiment 2
[0041] Example 2, taking a 12T coal-fired boiler as an example, when the boiler produces the same amount of water vapor, the comparison results of the relevant parameters of the new combustion system of the coal-fired boiler and the relevant parameters of the existing combustion system are shown in Table 2 :
[0042] Table 2
[0043] Combustion system related parameters existing combustion system this invention Coal seam thickness 14-16 cm about 9 cm Feeding frequency 40-50Hz 35-45Hz Blower power 37-45kW 5.5kW Induced fan power 90-110kW 11kW
Embodiment 3
[0044] Example 3, taking a 20T coal-fired boiler as an example, when the boiler produces the same amount of water vapor, the comparison results of the relevant parameters of the coal-fired boiler using the new combustion system and the relevant parameters of the existing combustion system are shown in Table 3 :
[0045] table 3
[0046] Combustion system related parameters existing combustion system this invention Coal seam thickness 16-19 cm about 11 cm Feeding frequency 40-50Hz 35-45Hz Blower power 55kW-70kW 7.5kW Induced fan power 120-150kW 20kW
[0047] The flue gas treatment device 8 includes a connected denitration device 8-1, a deammonization device 8-2, a wet electrostatic precipitator 8-3 and a denitrification device 8-4. The flue gas treatment device 8 also includes a desulfurizer and the like.
[0048] The steam generator 5 is connected with an automatic water supply device 6 .
[0049]The steam generator 5 is...
PUM
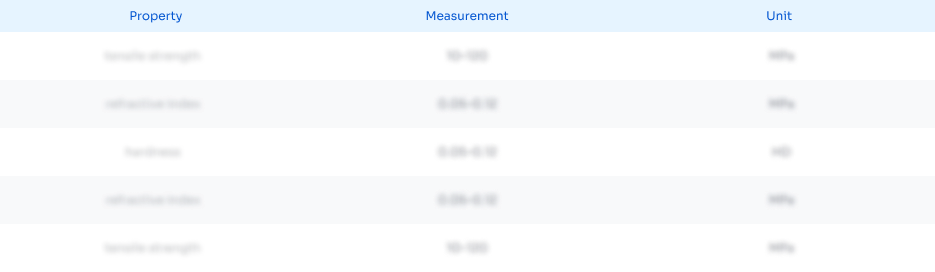
Abstract
Description
Claims
Application Information

- R&D
- Intellectual Property
- Life Sciences
- Materials
- Tech Scout
- Unparalleled Data Quality
- Higher Quality Content
- 60% Fewer Hallucinations
Browse by: Latest US Patents, China's latest patents, Technical Efficacy Thesaurus, Application Domain, Technology Topic, Popular Technical Reports.
© 2025 PatSnap. All rights reserved.Legal|Privacy policy|Modern Slavery Act Transparency Statement|Sitemap|About US| Contact US: help@patsnap.com