Reciprocating production process of electroplated copper-clad aluminum
A production process, a round-trip technology, applied in the field of metallurgy, can solve the problems of waste of resources, difficult to control, low copper content, etc., and achieve the effect of small improvement, significant optimization effect, and improved bonding strength.
- Summary
- Abstract
- Description
- Claims
- Application Information
AI Technical Summary
Problems solved by technology
Method used
Image
Examples
Embodiment 1
[0079] A production process for reciprocating electroplating copper-clad aluminum, comprising:
[0080] 1) Multi-stage alkali cleaning: the temperature is controlled at 60°C, and the aluminum base material is subjected to three times of alkali cleaning, and the alkali cleaning is carried out by countercurrent rinsing;
[0081] After the multi-stage alkali washing, the aluminum base material is washed with water, and the washing process is followed by a deionized water rinse and a deionized water countercurrent rinse; the lye contains 30g / L sodium hydroxide and 15g / L sodium phosphate, and the solvent is water;
[0082] 2) Zinc-precipitating treatment: Carry out zinc-precipitating twice on the cleaned aluminum material, during the zinc-precipitating process, the zinc-precipitating liquid is used as the aluminum alloy cyanide-free zinc-precipitating agent;
[0083] The zinc-precipitating process includes: sending the cleaned aluminum material into the zinc-precipitating tank, and...
Embodiment 2
[0097] A production process for reciprocating electroplating copper-clad aluminum, comprising:
[0098] 1) Multi-stage alkali cleaning: the temperature is controlled at 80°C, and the aluminum base material is subjected to three times of alkali cleaning, and the alkali cleaning is carried out by countercurrent rinsing;
[0099] After the multi-stage alkali washing, the aluminum base material is washed with water. The washing process is followed by a deionized water rinse and a deionized water countercurrent rinse; the alkali solution contains 25g / L of sodium hydroxide and 12.5g / L of sodium phosphate, and the solvent is water;
[0100] 2) Zinc-precipitating treatment: Carry out zinc-precipitating twice on the cleaned aluminum material, during the zinc-precipitating process, the zinc-precipitating liquid is used as the aluminum alloy cyanide-free zinc-precipitating agent;
[0101] The zinc precipitation is as follows: the cleaned aluminum material is sent to the zinc precipitatio...
Embodiment 3
[0115] A production process for reciprocating electroplating copper-clad aluminum, comprising:
[0116] 1) Multi-stage alkali cleaning: the temperature is controlled at 80°C, and the aluminum base material is subjected to three times of alkali cleaning, and the alkali cleaning is carried out by countercurrent rinsing;
[0117] After the multi-stage alkali washing, the aluminum base material is washed with water. The washing process is followed by a deionized water rinse and a deionized water countercurrent rinse; the alkali solution contains 25g / L of sodium hydroxide and 12.5g / L of sodium phosphate, and the solvent is water;
[0118] 2) Zinc-precipitating treatment: Carry out zinc-precipitating twice on the cleaned aluminum material, during the zinc-precipitating process, the zinc-precipitating liquid is used as the aluminum alloy cyanide-free zinc-precipitating agent;
[0119] Said zinc precipitation is: put the cleaned aluminum into the zinc precipitation tank, control the t...
PUM
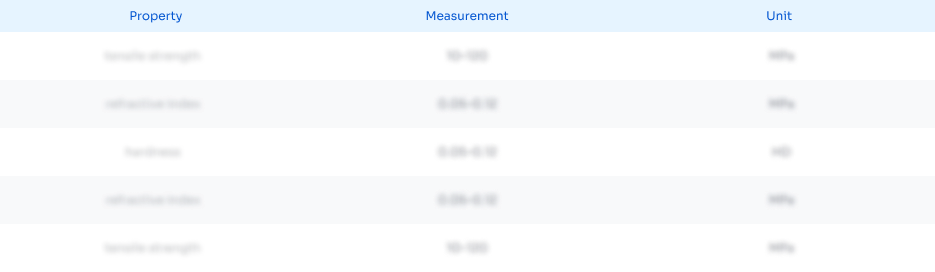
Abstract
Description
Claims
Application Information

- R&D Engineer
- R&D Manager
- IP Professional
- Industry Leading Data Capabilities
- Powerful AI technology
- Patent DNA Extraction
Browse by: Latest US Patents, China's latest patents, Technical Efficacy Thesaurus, Application Domain, Technology Topic, Popular Technical Reports.
© 2024 PatSnap. All rights reserved.Legal|Privacy policy|Modern Slavery Act Transparency Statement|Sitemap|About US| Contact US: help@patsnap.com