Two-step method for recycling melamine by degrading waste melamine resin
A melamine resin and melamine technology, applied in the direction of organic chemistry, etc., can solve the problems of not being able to recover all components of waste melamine resin and high energy consumption, and achieve strong technical operability, no secondary pollution, and mild reaction conditions. Effect
- Summary
- Abstract
- Description
- Claims
- Application Information
AI Technical Summary
Problems solved by technology
Method used
Image
Examples
Embodiment 1
[0030] Step 1, crush 1g of waste melamine resin into pellets with a particle size of 0.05mm, add tetrahydrofuran (the mass ratio of tetrahydrofuran to waste melamine resin is 1:1) to swell the waste melamine resin, and swell at 20°C 6h, making the melamine resin swelling and fluffy.
[0031] Step 2, immerse the swollen waste melamine resin into the HCl-water and ethanol system, and degrade it in a pressure vessel at 100°C for 12h under its own pressure (the mass ratio of HCl to the swollen waste melamine resin is 1:1; solvent and The mass ratio of the waste and old melamine resin after swelling is 1:1, and the volume ratio of water and ethanol in the solvent is 1:1), so that the melamine resin is degraded, the filter cake is washed with distilled water after filtration, reclaims and obtains melamine 0.8g, and collects the filtrate Can be recycled. The infrared spectrum of melamine is detailed in figure 1 , the wave number at 1840 corresponds to the C=N double bond on the mel...
Embodiment 2
[0033] Step 1, 1g waste and old melamine resin is pulverized into the particle diameter and is the pellet of 0.1mm, adds dichloromethane (the mass ratio of dichloromethane and waste and old melamine resin is 10:1) waste and old melamine resin is swelled, in Swell at 30°C for 6 hours, making the melamine resin swell and fluffy.
[0034] Step 2, immerse the swollen waste melamine resin in HNO 3 -Water, DMSO system, degrade for 10h under the self-pressure of the pressure vessel at 120°C (HNO 3 The mass ratio of the waste and old melamine resin after swelling is 1:2; the mass ratio of the solvent and the swelling of the waste and old melamine resin is 100:1, and the volume ratio of water and DMSO in the solvent is 1:1.5), so that the melamine The resin was degraded, and after filtration, the filter cake was washed with distilled water to recover 0.82 g of melamine.
Embodiment 3
[0036] Step 1, crush 1g of waste melamine resin into pellets with a particle size of 0.2mm, add chloroform (the mass ratio of chloroform to waste melamine resin is 20:1) to swell the waste melamine resin, and swell at 50°C 5h, making the melamine resin swelling and fluffy.
[0037] Step 2, immerse the waste melamine resin after swelling in H 2 SO 4 -Water, dichloromethane system, degrade for 9h (H 2 SO 4 The mass ratio with the waste and old melamine resin after swelling is 1:3; The mass ratio of solvent and the waste and old melamine resin after swelling is 30:1, and the volume ratio of water and dichloromethane in the solvent is 1:2), making The melamine resin was degraded, and after filtration, the filter cake was washed with distilled water to recover 0.78 g of melamine.
PUM
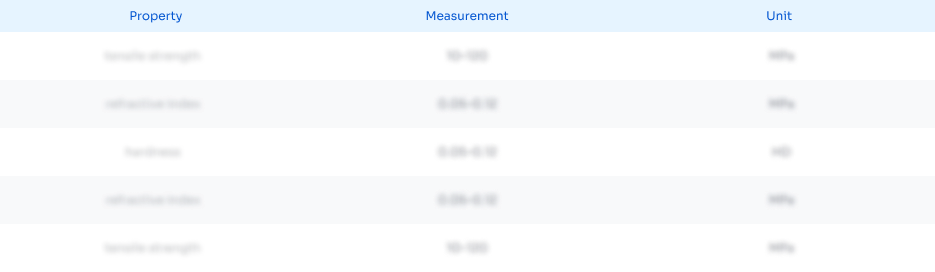
Abstract
Description
Claims
Application Information

- R&D
- Intellectual Property
- Life Sciences
- Materials
- Tech Scout
- Unparalleled Data Quality
- Higher Quality Content
- 60% Fewer Hallucinations
Browse by: Latest US Patents, China's latest patents, Technical Efficacy Thesaurus, Application Domain, Technology Topic, Popular Technical Reports.
© 2025 PatSnap. All rights reserved.Legal|Privacy policy|Modern Slavery Act Transparency Statement|Sitemap|About US| Contact US: help@patsnap.com