Unmanned carrying automated guided vehicle and guiding method thereof
An automatic guided vehicle and vehicle body technology, applied in the direction of lifting devices, etc., can solve the problems of poor stability and easy slipping, and achieve the effect of good stability, not easy to slip, and small size
- Summary
- Abstract
- Description
- Claims
- Application Information
AI Technical Summary
Problems solved by technology
Method used
Image
Examples
Embodiment 1
[0063] see Figure 1-7 , this embodiment provides an unmanned automatic guided vehicle, which can be called a mini unmanned AGV, which is mainly used to carry goods or materials, and does not need to be driven. Wherein, the unmanned automatic guided vehicle includes a car body 1, a fork leg 2, a driving wheel mechanism 3, a driven wheel mechanism 4, a hydraulic system 5 and an electric control system.
[0064] The car body 1 is the main part of the automatic guided vehicle. In this embodiment, the car body 1 is a shell structure, and other parts can be installed inside it. The car body 1 can adopt the car body 1 of existing AGV, and its specific size and shape can be set according to actual needs. Round corner design can be carried out around the car body 1, which can prevent the car body 1 from colliding with other objects and being damaged during driving. The surface of the vehicle body 1 can be coated with wear-resistant materials or other materials.
[0065] The number ...
Embodiment 2
[0084] This embodiment provides an unmanned automatic guided vehicle, which is similar to the unmanned automatic guided vehicle in Embodiment 1, except that the control unit 71 also has other functions. Wherein, the control unit 71 is used for judging whether the distance is smaller than a set threshold. When the distance is less than the set threshold, the control unit 71 drives the driving wheel mechanism 3 to stop, so as to protect the AGV from bumping into obstacles during operation, which can not only protect the automatic guided vehicle from damage, but also protect the moving path of the automatic guided vehicle surrounding objects.
Embodiment 3
[0086] This embodiment provides a cargo handling system, which includes a plurality of mini unmanned handling AGVs, and these mini unmanned handling AGVs cooperate with each other to transport a large amount of goods from different locations to the same point or multiple target locations. Wherein, the mini unmanned transport AGV is the unmanned transport automatic guided vehicle in embodiment 1 or embodiment 2. The path planning method between these mini unmanned handling AGVs adopts the existing path avoidance and operation mode between AGVs.
PUM
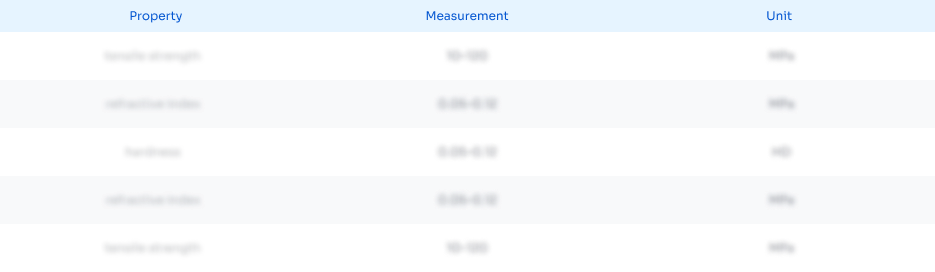
Abstract
Description
Claims
Application Information

- Generate Ideas
- Intellectual Property
- Life Sciences
- Materials
- Tech Scout
- Unparalleled Data Quality
- Higher Quality Content
- 60% Fewer Hallucinations
Browse by: Latest US Patents, China's latest patents, Technical Efficacy Thesaurus, Application Domain, Technology Topic, Popular Technical Reports.
© 2025 PatSnap. All rights reserved.Legal|Privacy policy|Modern Slavery Act Transparency Statement|Sitemap|About US| Contact US: help@patsnap.com