Chlorine ion corrosion-resistant steel rail and preparation method
A chloride ion corrosion and rail technology, applied in the field of metal material production, can solve the problems of shortening rail replacement cycle, reducing rail support strength, increasing rail maintenance and inspection costs, etc., to ensure the safety of passenger production and property, and reduce maintenance and replacement costs , The effect of promoting the development of the railway industry
- Summary
- Abstract
- Description
- Claims
- Application Information
AI Technical Summary
Problems solved by technology
Method used
Image
Examples
Embodiment 1
[0030] The components and weight percentages of the steel rails resistant to chloride ion corrosion include C: 0.68%, Si: 0.66%, Mn: 1.02%, P: 0.005%, S: 0.002%, Nb: 0.026%, Als: 0.002%, Cr: 1.28%, Cu: 2.7%, Co: 0.49%, H: 0.00005%, O: 0.0004%, and the rest are Fe and impurity elements.
[0031] 1) Carry out deep desulfurization of molten iron, use converter smelting, and control the tapping temperature at 1661°C;
[0032] 2) Add 46kg of active lime to each ton of molten steel to make white slag for deep deoxidation and desulfurization, then add 37kg of quartz sand to each ton of molten steel, control the slag basicity at 0.8, and LF furnace treatment time for 53min to turn inclusions in steel into plastic inclusions;
[0033] 3) RH vacuum dehydrogenation and oxygen treatment: use low vacuum degree, the treatment time is 26min with pressure ≤ 40Pa;
[0034] 4) For continuous casting of molten steel, the long nozzle of the large tank and the submerged nozzle of the crystallizer...
Embodiment 2
[0041] The components and weight percentages of steel rails resistant to chloride ion corrosion include C: 0.71%, Si: 0.58%, Mn: 0.95%, P: 0.003%, S: 0.002%, Nb: 0.023%, Als: 0.001%, Cr: 1.37 %, Cu: 2.7%, Co: 0.49%, H: 0.00005%, O: 0.0004%, and the rest are Fe and impurity elements.
[0042] 1) Carry out deep desulfurization of molten iron, use converter smelting, and control the tapping temperature at 1666°C;
[0043] 2) Add 48kg of active lime to each ton of molten steel to make white slag for deep deoxidation and desulfurization, then add 39kg of quartz sand to each ton of molten steel, control the slag alkalinity at 0.9, and LF furnace for 55 minutes to turn the inclusions in the steel into plastic inclusions;
[0044] 3) RH vacuum dehydrogenation and oxygen treatment: use low vacuum degree, the treatment time is 23min with pressure ≤ 40Pa;
[0045] 4) For continuous casting of molten steel, the long nozzle of the large tank and the submerged nozzle of the crystallizer are ...
Embodiment 3
[0052] The components and weight percentages of steel rails resistant to chloride ion corrosion include C: 0.73%, Si: 0.62%, Mn: 1.36%, P: 0.004%, S: 0.001%, Nb: 0.028%, Als: 0.002%, Cr: 1.78 %, Cu: 3.1%, Co: 0.51%, H: 0.000035%, O: 0.0002%, and the rest are Fe and impurity elements.
[0053] 1) Carry out deep desulfurization of molten iron, use converter smelting, and control the tapping temperature at 1669°C;
[0054] 2) Add 50kg of active lime to each ton of molten steel to make white slag for deep deoxidation and desulfurization, then add 41kg of quartz sand to each ton of molten steel, control the slag alkalinity at 1.0, and use the LF furnace for 55 minutes to transform inclusions in steel into plastic inclusions;
[0055] 3) RH vacuum dehydrogenation and oxygen treatment: use low vacuum degree, the treatment time is 25min with pressure ≤ 40Pa;
[0056] 4) For continuous casting of molten steel, the long nozzle of the large tank and the submerged nozzle of the crystalli...
PUM
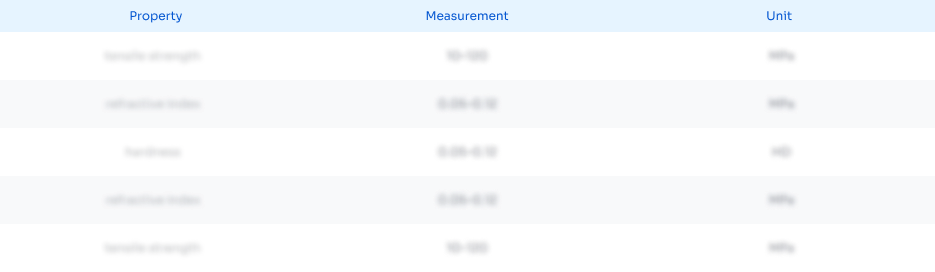
Abstract
Description
Claims
Application Information

- Generate Ideas
- Intellectual Property
- Life Sciences
- Materials
- Tech Scout
- Unparalleled Data Quality
- Higher Quality Content
- 60% Fewer Hallucinations
Browse by: Latest US Patents, China's latest patents, Technical Efficacy Thesaurus, Application Domain, Technology Topic, Popular Technical Reports.
© 2025 PatSnap. All rights reserved.Legal|Privacy policy|Modern Slavery Act Transparency Statement|Sitemap|About US| Contact US: help@patsnap.com