Titanium and titanium alloy surface hardening and surface functionalization process
A technology of surface functionalization and treatment process, which is applied in the direction of metal material coating process, heating inorganic powder coating, coating, etc., can solve the problems of large product size limitation, difficult to obtain coating, and difficult promotion, etc., to achieve The effect of simple production equipment, low production cost and wide range of options
- Summary
- Abstract
- Description
- Claims
- Application Information
AI Technical Summary
Problems solved by technology
Method used
Image
Examples
Embodiment 1
[0037] 1. Put the titanium alloy block (Ti-6Al-4V) into figure 1 As shown in the stainless steel mold, the gap between the mold and the titanium alloy block is at the top of the cylindrical cavity, and the thickness is 5mm. The mixed powder containing 80% titanium powder and 20% carbon fiber is evenly filled in the mold, and the mold is packaged and fastened.
[0038] 2. Put the assembled mold into an atmosphere sintering furnace, heat it to 800°C under an argon atmosphere, and keep it warm for one hour; inject hydrogen (hydrogen gas flow rate is 1L / min), and cool down to 600°C at a rate of 1°C / min. Keep feeding hydrogen and keep it warm for 4 hours, and the furnace is cold.
[0039] 3. Turn to vacuum sintering furnace, vacuumize (vacuum degree is less than 10 -3 Pa), raise the temperature to 750° C., keep the furnace for 4 hours, and then stop the furnace for cooling.
[0040] 4. Open the vacuum sintering furnace, take out and open the mold, continue to put the sample into ...
Embodiment 2
[0043]1. Put the titanium alloy block (Ti-6Al-4V) into figure 1 The stainless steel mold shown, the gap between the mold and the titanium alloy block is at the top of the cylindrical cavity, the thickness is 5mm, and it will contain 94% titanium powder, 6% B 4 The mixed powder of C is evenly filled in the mold, and the mold is sealed and fastened.
[0044] 2. Put the assembled mold into an atmosphere sintering furnace, heat it to 800°C under an argon atmosphere, and keep it warm for one hour; inject hydrogen (hydrogen gas flow rate is 1L / min), and cool down to 600°C at a rate of 1°C / min. Keep feeding hydrogen and keep it warm for 4 hours, and the furnace is cold.
[0045] 3. Turn to vacuum sintering furnace, vacuumize (vacuum degree is less than 10 -3 Pa), raise the temperature to 750° C., keep the furnace for 4 hours, and then stop the furnace for cooling.
[0046] 4. Open the vacuum sintering furnace, take out and open the mold, continue to put the sample into the vacuum ...
Embodiment 3
[0049] 1. Put the titanium alloy block (Ti-6Al-4V) into a stainless steel mold, the gap between the mold and the titanium alloy block is the side of the cylinder, the thickness is 2mm, and the mixed powder containing 92% titanium powder and 8% graphite is placed in the mold Fill the mold evenly, seal and fasten the mold.
[0050] 2. Put the assembled mold into an atmosphere sintering furnace, heat it to 800°C under an argon atmosphere, and keep it warm for one hour; inject hydrogen (hydrogen gas flow rate is 1L / min), and cool down to 600°C at a rate of 1°C / min. Keep feeding hydrogen and keep it warm for 4 hours, and the furnace is cold.
[0051] 3. Turn to vacuum sintering furnace, vacuumize (vacuum degree is less than 10 -3 Pa), raise the temperature to 750° C., keep the furnace for 4 hours, and then stop the furnace for cooling.
[0052] 4. Open the vacuum sintering furnace, take out and open the mold, continue to put the sample into the vacuum sintering furnace, vacuumize...
PUM
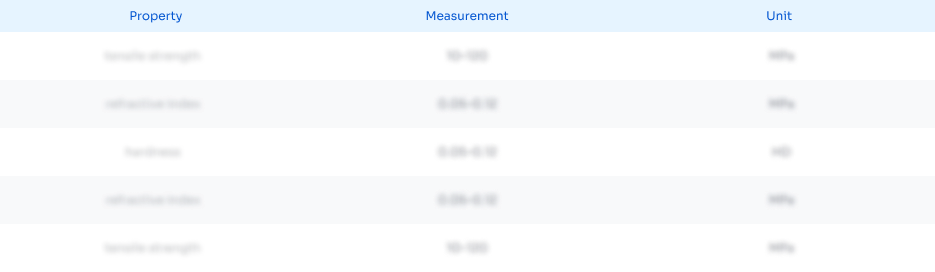
Abstract
Description
Claims
Application Information

- Generate Ideas
- Intellectual Property
- Life Sciences
- Materials
- Tech Scout
- Unparalleled Data Quality
- Higher Quality Content
- 60% Fewer Hallucinations
Browse by: Latest US Patents, China's latest patents, Technical Efficacy Thesaurus, Application Domain, Technology Topic, Popular Technical Reports.
© 2025 PatSnap. All rights reserved.Legal|Privacy policy|Modern Slavery Act Transparency Statement|Sitemap|About US| Contact US: help@patsnap.com