High-temperature-resistant coating layer on graphite base material and preparation method of high-temperature-resistant coating layer
A technology of graphite base material and high temperature resistance, applied in the field of graphite, can solve the problems of inability to meet the oxidation resistance requirements of graphite materials, poor bonding between the coating and the substrate, and insufficient air tightness of the coating, so as to facilitate industrial production and application, and is not easy Good effect of shedding and air tightness
- Summary
- Abstract
- Description
- Claims
- Application Information
AI Technical Summary
Problems solved by technology
Method used
Image
Examples
Embodiment 1
[0028] (1) Choose a graphite substrate, polish the surface and perform ultrasonic treatment with absolute ethanol, put it in an oven after the surface is dry, and place it at 100° C. for 2 hours, and wait for use.
[0029] (2) Weigh 5g of polyvinylpyrrolidone as a binder, and dissolve it into 35ml of absolute ethanol for 30min ultrasonic treatment. After completion, add 4g of silicon carbide, 1.5g of hafnium boride, 4g of zirconium boride, 2g of tungsten powder, 0.2 g silicon powder, carry out ultrasonic treatment of 60min, to obtain the slurry of silicon carbide composite coating;
[0030] (3) Put the treated graphite sample into the prepared slurry and perform ultrasonication for 10 minutes, so that the surface is fully adsorbed with a uniform silicon carbide coating material;
[0031] (4) After the graphite sample is taken out from the slurry and left to dry, put it into an oven and carry out a preheating treatment at 100°C;
[0032] (5) Prepare the embedding powder that i...
Embodiment 2
[0035] (1) Choose a graphite substrate, polish the surface and ultrasonically clean it once with acetone and alcohol respectively, and place it in an oven at 60°C for 4 hours until use.
[0036] (2) Weigh 8g of phenolic resin as a binder, and dissolve it into 50ml of absolute ethanol for 30min ultrasonic treatment. After completion, add 6g of silicon carbide, 2.5g of hafnium boride, 5g of zirconium boride, 3g of tungsten powder, 0.5g Silicon powder, add magnets, and carry out magnetic stirring for 60 minutes to obtain the slurry of silicon carbide composite coating;
[0037] (3) Evenly brush the prepared slurry on the surface of the graphite sample, let it stand to dry, then brush again, repeat 2 times, put it into an oven at 200°C after completion, and carry out 1h preheating treatment;
[0038] (4) Prepare the embedding powder that isolates oxygen at high temperature and plays a protective role. Weigh 6g of silicon carbide, 0.5g of carbon powder, 3g of zirconium boride, 0.4g...
PUM
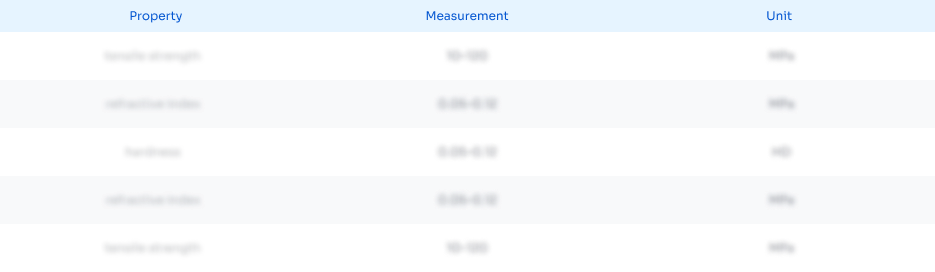
Abstract
Description
Claims
Application Information

- Generate Ideas
- Intellectual Property
- Life Sciences
- Materials
- Tech Scout
- Unparalleled Data Quality
- Higher Quality Content
- 60% Fewer Hallucinations
Browse by: Latest US Patents, China's latest patents, Technical Efficacy Thesaurus, Application Domain, Technology Topic, Popular Technical Reports.
© 2025 PatSnap. All rights reserved.Legal|Privacy policy|Modern Slavery Act Transparency Statement|Sitemap|About US| Contact US: help@patsnap.com