Thinning process of optocoupler packaging lead frame material
A technology of lead frame and packaging lead, which is applied in the direction of stripping devices, manufacturing tools, metal processing equipment, etc., can solve the problems of product storage such as moisture absorption and oxidation, achieve significant production practical significance, avoid oxidation problems, and reduce the effect of exposed copper areas
- Summary
- Abstract
- Description
- Claims
- Application Information
AI Technical Summary
Problems solved by technology
Method used
Image
Examples
Embodiment Construction
[0021] The present invention will be further described below in conjunction with the accompanying drawings.
[0022] see Figure 1 to Figure 3 As shown, the present invention provides an embodiment: a thinning process of an optocoupler package lead frame material includes the following steps:
[0023] Step S1, install the stamping die into the hydraulic punching machine, and fix the upper and lower dies respectively;
[0024] Step S2, placing the uncut lead frame material 1 roll on the feed end of the punch press;
[0025] Step S3, fixing the lead frame element material head to the entrance of the stamping die;
[0026] Step S4, after the lead frame material 1 is fixed, the punch press performs the first mold clamping stamping;
[0027] Step S5, Punch the lead frame material 1 out of the positioning holes on both sides. After the positioning holes are punched out, the staff will open the mold. The lead frame material puts the positioning pin into the "upper side" of the fr...
PUM
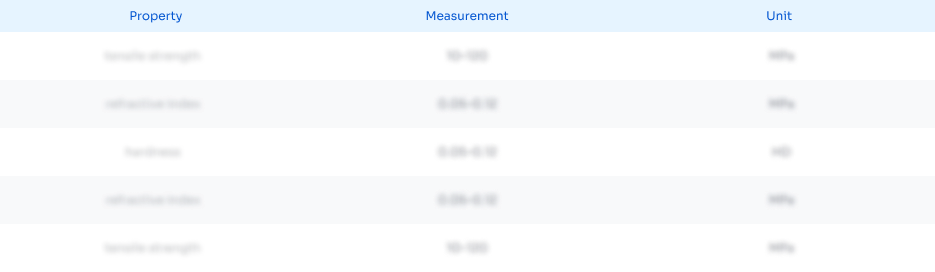
Abstract
Description
Claims
Application Information

- R&D
- Intellectual Property
- Life Sciences
- Materials
- Tech Scout
- Unparalleled Data Quality
- Higher Quality Content
- 60% Fewer Hallucinations
Browse by: Latest US Patents, China's latest patents, Technical Efficacy Thesaurus, Application Domain, Technology Topic, Popular Technical Reports.
© 2025 PatSnap. All rights reserved.Legal|Privacy policy|Modern Slavery Act Transparency Statement|Sitemap|About US| Contact US: help@patsnap.com