Low-pressure vacuum carburizing method for 10CrNi2Mo3Cu2V material
A vacuum carburizing and low-pressure technology, which is applied in the direction of metal material coating process, coating, solid-state diffusion coating, etc., can solve the problems of poor repeatability and achieve the effect of improving repeatability and ensuring consistency
- Summary
- Abstract
- Description
- Claims
- Application Information
AI Technical Summary
Problems solved by technology
Method used
Image
Examples
Embodiment 1
[0022] Aviation gears for helicopter reducers are made of second-generation carburized gear steel 10CrNi2Mo3Cu2V, and the effective carburized layer depth after carburizing is 0.70-0.90mm. It is necessary to ensure the consistency of the carburizing layer depth of multiple carburizing batches. The specific implementation method is as follows:
[0023] Place the parts in a low-pressure vacuum carburizing furnace for carburizing, adopt the pulse carburizing method, and set the pulse intensive carburizing stage time t c For a fixed value, after carburizing, push it to the front room and air cool it.
[0024] The time t of the set pulse hyperosmotic phase c The value range is 0.7min, the pulse carburizing is adopted, and the number of pulses is 16. Each pulse first performs pulse infiltration, and then performs pulse diffusion. The diffusion time of the latter pulse is longer than that of the previous pulse. , the pulse diffusion time is greater than the pulse infiltration time,...
Embodiment 2
[0030] The aviation gear used for a helicopter reducer is made of second-generation carburized gear steel 10CrNi2Mo3Cu2V, and the effective carburized layer depth after carburizing is 0.90-1.10mm. It is necessary to ensure the consistency of the carburizing layer depth of multiple carburizing batches. The specific implementation method is as follows:
[0031] Place the parts in a low-pressure vacuum carburizing furnace for carburizing, adopt the pulse carburizing method, and set the pulse intensive carburizing stage time t c For a fixed value, after carburizing, push it to the front room and air cool it.
[0032] The time t of the set pulse hyperosmotic phase c The value range is 0.7min.
[0033] The pulse carburizing is adopted, the number of pulses is 16, and the effective depth of the carburizing layer is 0.90-1.10mm.
[0034] In the pulse carburizing described above, each pulse first performs pulse intensive infiltration, and then performs pulse diffusion.
[0035] The...
PUM
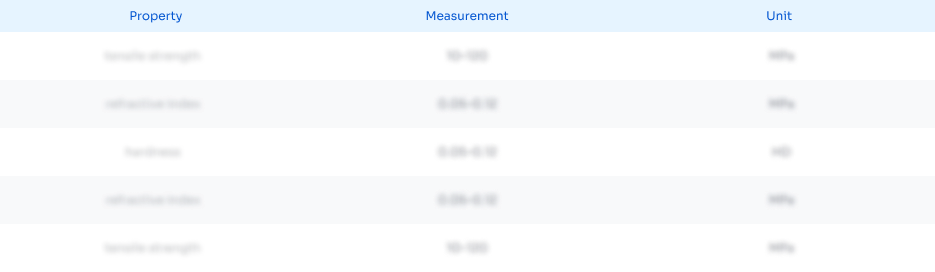
Abstract
Description
Claims
Application Information

- Generate Ideas
- Intellectual Property
- Life Sciences
- Materials
- Tech Scout
- Unparalleled Data Quality
- Higher Quality Content
- 60% Fewer Hallucinations
Browse by: Latest US Patents, China's latest patents, Technical Efficacy Thesaurus, Application Domain, Technology Topic, Popular Technical Reports.
© 2025 PatSnap. All rights reserved.Legal|Privacy policy|Modern Slavery Act Transparency Statement|Sitemap|About US| Contact US: help@patsnap.com