110KV intermediate head and production process thereof
A technology for intermediate joints and production processes, which is applied in the direction of cable joints, connections, electrical components, etc., can solve problems such as inability to directly inspect with the naked eye, difficult pressure control, low yield, etc., to achieve visual inspection, easy inspection, high visibility effect
- Summary
- Abstract
- Description
- Claims
- Application Information
AI Technical Summary
Problems solved by technology
Method used
Image
Examples
Embodiment Construction
[0031] The present invention will be further described below in conjunction with the accompanying drawings and embodiments.
[0032] Such as figure 1 As shown, in the production process of an intermediate joint above 110KV, the requirements for the production environment are relatively strict. If it is produced in an ordinary environment, the dust in the air will pollute the rubber body, because the product is injection molded multiple times and installed in the mold. When the parts are directly exposed to the air, the surface of the mold and the rubber body will be contaminated with dust in the air, and the glue will be mixed in the liquid rubber when it is injected, and it will stay in the rubber body after vulcanization, especially the insulating silicone rubber. The silicone rubber body contains too many impurities, which will seriously affect the electrical properties of the rubber, cause partial discharge, and affect the service life of the intermediate joint. In serious...
PUM
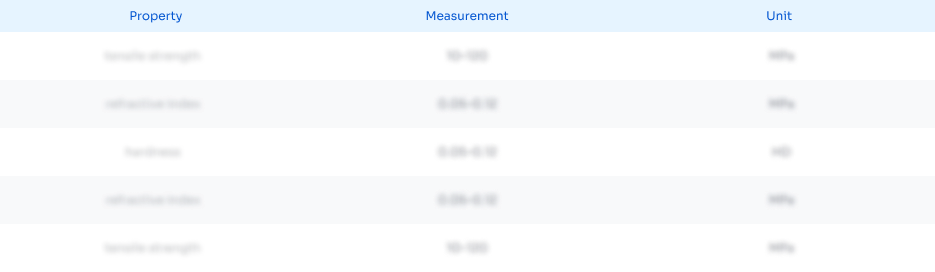
Abstract
Description
Claims
Application Information

- R&D
- Intellectual Property
- Life Sciences
- Materials
- Tech Scout
- Unparalleled Data Quality
- Higher Quality Content
- 60% Fewer Hallucinations
Browse by: Latest US Patents, China's latest patents, Technical Efficacy Thesaurus, Application Domain, Technology Topic, Popular Technical Reports.
© 2025 PatSnap. All rights reserved.Legal|Privacy policy|Modern Slavery Act Transparency Statement|Sitemap|About US| Contact US: help@patsnap.com