Method for preparing copper-iron alloy nanopowder
A technology of copper-iron alloy and nano-powder is applied in the field of preparation of copper-iron alloy nano-powder, which can solve the problems such as unreported preparation of nano-powder, and achieve the effects of eliminating sieving and classification, reducing particle size range and improving ignition effect.
- Summary
- Abstract
- Description
- Claims
- Application Information
AI Technical Summary
Problems solved by technology
Method used
Image
Examples
Embodiment 1
[0040] In terms of percentage content, the percentage content of Fe element in the raw material is 5%, wherein Fe element is added in the form of CuFe master alloy;
[0041] Select an alumina crucible, control the vacuum degree р≤4Pa during melting; melt at a temperature of 1200°C, melt until the solution is melted, vacuum pour it into a water-cooled copper mold, and solidify into a copper-iron alloy ingot;
[0042] The copper-iron alloy ingot in step S2 is prepared into a Φ1.5mm wire through multi-pass drawing;
[0043] Vacuumize the electric explosion chamber, and the vacuum degree is lower than 5Pa;
[0044] The wire feeder feeds the prepared Φ1.5mm copper and iron wire between the anode and cathode of the electric explosion chamber, and then fills it with argon gas for protection and as a coolant for backup. The gas pressure is 0.2Mpa, and 3×10 5 V high-voltage electricity, the wire material instantly reaches a high temperature of tens of thousands of degrees, explodes af...
Embodiment 2
[0047] In terms of percentage content, the percentage content of Fe element in the raw material is 5%, wherein Fe element is added in the form of CuFe master alloy;
[0048] Choose an alumina crucible, control the vacuum degree р≤4Pa during melting; melt at a temperature of 1300°C, melt until the solution is melted, and vacuum pour it into a water-cooled copper mold to solidify into a copper-iron alloy ingot;
[0049] The copper-iron alloy ingot in step S2 is prepared into a Φ1.5mm wire through multi-pass drawing;
[0050] Vacuumize the electric explosion chamber, and the vacuum degree is lower than 5Pa;
[0051] The wire feeder sends the prepared Φ1.5mm copper and iron wire between the anode and cathode of the electric explosion chamber, and then fills it with argon gas for protection and as a coolant for backup. The gas pressure is 0.3Mpa, and 4×10 5 V high-voltage electricity, the wire material instantly reaches a high temperature of tens of thousands of degrees, explodes ...
Embodiment 3
[0054] In terms of percentage content, the percentage content of Fe element in the raw material is 10%, wherein Fe element is added in the form of CuFe master alloy;
[0055] Choose a zirconia crucible, control the vacuum degree р≤4Pa during melting; melt at a temperature of 1400°C, melt until the solution is melted, vacuum pour it into a water-cooled copper mold, and solidify into a copper-iron alloy ingot;
[0056] The copper-iron alloy ingot in step S2 is prepared into a Φ1.5mm wire through multi-pass drawing;
[0057] Vacuumize the electric explosion chamber, and the vacuum degree is lower than 5Pa;
[0058] The wire feeder sends the prepared Φ1.5mm copper and iron wire between the anode and cathode of the electric explosion chamber, and then fills it with argon gas for protection and as a coolant for backup. The gas pressure is 0.3Mpa, and the release is 3.5×10 5 V high-voltage electricity, the wire material instantly reaches a high temperature of tens of thousands of degr...
PUM
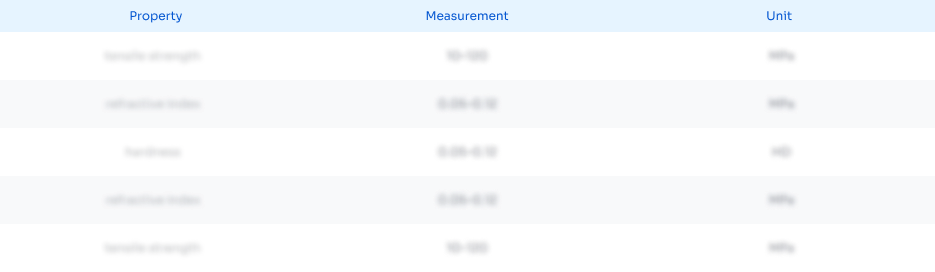
Abstract
Description
Claims
Application Information

- R&D Engineer
- R&D Manager
- IP Professional
- Industry Leading Data Capabilities
- Powerful AI technology
- Patent DNA Extraction
Browse by: Latest US Patents, China's latest patents, Technical Efficacy Thesaurus, Application Domain, Technology Topic, Popular Technical Reports.
© 2024 PatSnap. All rights reserved.Legal|Privacy policy|Modern Slavery Act Transparency Statement|Sitemap|About US| Contact US: help@patsnap.com