3D dazzling ceramic tile and preparation method thereof
A ceramic tile and glare technology, applied in the field of architectural ceramics, can solve problems such as poor color development, and achieve the effects of being conducive to large-scale industrial production, strong controllability, and broadening the scope of application
- Summary
- Abstract
- Description
- Claims
- Application Information
AI Technical Summary
Problems solved by technology
Method used
Examples
Embodiment 1
[0025] A 3D three-dimensional glare ceramic tile, which comprises a body layer, a glare surface glaze layer, an inkjet pattern texture layer, a peeling glaze ink layer, and a transparent protective glaze layer from bottom to top.
[0026] The raw material components of the glare surface glaze in the glare surface glaze layer include 35 parts by weight of albite, 15 parts of kaolin, 11 parts of barium carbonate, 2 parts of zinc oxide, 16 parts of quartz, 4 parts of aluminum oxide, 5 parts of calcined kaolin, 10 parts of inkjet frit; the raw material components of the transparent protective glaze in the transparent protective glaze layer include 15 parts of potassium feldspar, 18 parts of albite feldspar, 13 parts of kaolin, and 8 parts of calcined talc in parts by weight. 5 parts, 5 parts of wollastonite, 22 parts of barium carbonate, 14 parts of dolomite, 4 parts of zinc oxide, 2 parts of aluminum oxide, 11 parts of transparent bright frit.
[0027] The ink-jet frit is calcula...
Embodiment 2
[0068] A 3D three-dimensional glare ceramic brick, which consists of a base body layer, a glare surface glaze layer, an inkjet pattern texture layer, a bleeding ink layer, and a transparent protective glaze layer from bottom to top.
[0069] The raw material components of the glare surface glaze in the glare surface glaze layer include 40 parts by weight of albite, 12 parts of kaolin, 15 parts of barium carbonate, 1 part of zinc oxide, 20 parts of quartz, 2 parts of aluminum oxide, 6 parts of calcined kaolin, 0.5 part of inkjet frit; the raw material components of the transparent protective glaze in the transparent protective glaze layer include 12 parts by weight of potassium feldspar, 24 parts of albite feldspar, 12 parts of kaolin, and 12 parts of calcined talc 3 parts, 3 parts of wollastonite, 26 parts of barium carbonate, 10 parts of dolomite, 6 parts of zinc oxide, 1 part of aluminum oxide, 6 parts of transparent bright frit.
[0070] The ink-jet frit is calculated by we...
Embodiment 3
[0079] A 3D three-dimensional glare ceramic brick, which consists of a body layer, a glare surface glaze layer, an inkjet pattern texture layer, a bright ink layer, and a transparent protective glaze layer from bottom to top.
[0080] The raw material components of the glare surface glaze in the glare surface glaze layer include 38 parts by weight of albite, 14 parts of kaolin, 12 parts of barium carbonate, 1.5 parts of zinc oxide, 18 parts of quartz, 3 parts of aluminum oxide, 5.5 parts of calcined kaolin, 6 parts of inkjet frit; the raw material components of the transparent protective glaze in the transparent protective glaze layer include 13 parts of potassium feldspar, 20 parts of albite feldspar, 12.5 parts of kaolin, and 10 parts of calcined talc in parts by weight. 4 parts, 4 parts of wollastonite, 25 parts of barium carbonate, 12 parts of dolomite, 5 parts of zinc oxide, 1.5 parts of aluminum oxide, 11.5 parts of transparent bright frit.
[0081] The ink-jet frit is c...
PUM
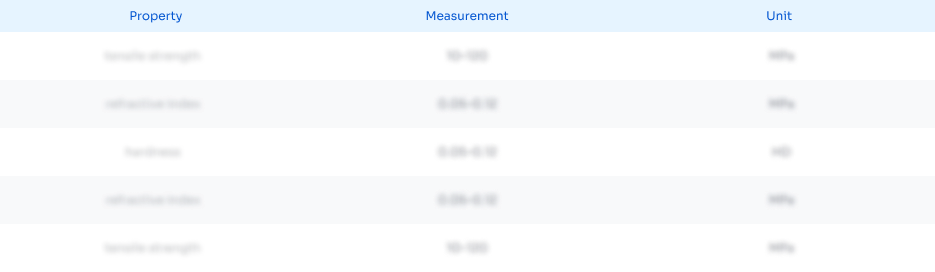
Abstract
Description
Claims
Application Information

- Generate Ideas
- Intellectual Property
- Life Sciences
- Materials
- Tech Scout
- Unparalleled Data Quality
- Higher Quality Content
- 60% Fewer Hallucinations
Browse by: Latest US Patents, China's latest patents, Technical Efficacy Thesaurus, Application Domain, Technology Topic, Popular Technical Reports.
© 2025 PatSnap. All rights reserved.Legal|Privacy policy|Modern Slavery Act Transparency Statement|Sitemap|About US| Contact US: help@patsnap.com