Processing technology of mirror surface aluminum alloy wheel hub
An aluminum alloy wheel hub, processing technology, applied in special surfaces, pretreatment surfaces, devices for coating liquids on surfaces, etc., can solve areas where mirror processing cannot be specified, low production efficiency of electroplating technology, environmental and human damage, etc. problem, to achieve the effect of enhancing the visual luxury level, enhancing the visual impact and high finish
- Summary
- Abstract
- Description
- Claims
- Application Information
AI Technical Summary
Problems solved by technology
Method used
Examples
Embodiment 1
[0023] 1. A kind of processing technology of mirror surface aluminum alloy wheel hub, it is characterized in that: comprise the following steps,
[0024] 1) Rough turning: Carbide cutting tools with a radius of 4.0 are used to process, remove the excess of the blank, and reserve a machining allowance of 0.2m, the spindle speed is controlled at 1600 rpm, and the tool feed rate is 0.3mm / change;
[0025] 2) Pre-finishing: use PCD tool with R3.0 tool nose radius for machining, finish the wheel hub surface after rough turning, reserve 0.1m machining allowance, control the spindle speed at 1600 rpm, The speed is 0.3mm / rev;
[0026] 3) Cleaning and drying: use a medium-temperature degreasing agent and a chrome-free passivator to clean the surface of the wheel hub after pre-finishing, and then dry it. The drying temperature is 110°C and the drying time is 40 minutes to remove the surface of the wheel hub. oil and other pollutants;
[0027] 4) Coating and curing: transfer the clean...
Embodiment 2
[0037] 1. A kind of processing technology of mirror surface aluminum alloy wheel hub, it is characterized in that: comprise the following steps,
[0038] 1) Rough turning: Carbide cutting tools with a radius of 4.0 are used to process, remove the excess of the blank, and reserve a machining allowance of 0.25m, the spindle speed is controlled at 1800 rpm, and the tool feed rate is 0.35mm / change;
[0039] 2) Pre-finishing: use PCD tool with R3.0 nose radius for machining, finish the wheel hub surface after rough turning, reserve 0.15m machining allowance, control the spindle speed at 1800 rpm, The feeding speed is 0.35mm / rev;
[0040] 3) Cleaning and drying: use a medium-temperature degreasing agent and a chrome-free passivator to clean the surface of the wheel hub after pre-finishing, and then dry it. The drying temperature is 120°C and the drying time is 35 minutes to remove the surface of the wheel hub. oil and other pollutants;
[0041] 4) Coating and curing: transfer th...
Embodiment 3
[0051] 1. A kind of processing technology of mirror surface aluminum alloy wheel hub, it is characterized in that: comprise the following steps,
[0052] 1) Rough turning: Carbide cutting tools with a radius of 4.0 are used to process, remove the excess of the rough blank, and reserve a machining allowance of 0.3m, the spindle speed is controlled at 2000 rpm, and the tool feed rate is 0.4mm / change;
[0053] 2) Pre-finishing: use PCD tools with a radius of R3.0 for machining, and finish the surface of the wheel hub after rough turning, reserve a machining allowance of 0.2m, and control the spindle speed at 2000 rpm. The feeding speed is 0.4mm / rev;
[0054] 3) Cleaning and drying: use a medium-temperature degreasing agent and a chrome-free passivator to clean the surface of the wheel hub after pre-finishing, and then dry it. The drying temperature is 130°C and the drying time is 30 minutes to remove the surface of the wheel hub. oil and other pollutants;
[0055] 4) Coating ...
PUM
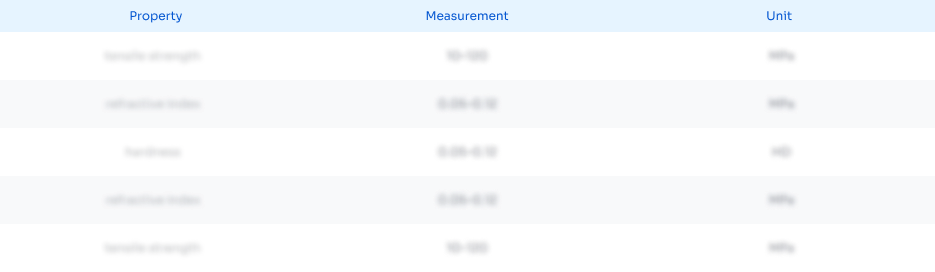
Abstract
Description
Claims
Application Information

- R&D
- Intellectual Property
- Life Sciences
- Materials
- Tech Scout
- Unparalleled Data Quality
- Higher Quality Content
- 60% Fewer Hallucinations
Browse by: Latest US Patents, China's latest patents, Technical Efficacy Thesaurus, Application Domain, Technology Topic, Popular Technical Reports.
© 2025 PatSnap. All rights reserved.Legal|Privacy policy|Modern Slavery Act Transparency Statement|Sitemap|About US| Contact US: help@patsnap.com