Method for extracting lithium from waste lithium ion battery anode material through pre-reduction and optimal solution
A lithium-ion battery and cathode material technology, which is applied in the field of hydrometallurgy, can solve the problems of increasing the amount of sodium hydroxide solution, affecting the quality of the final product, and high processing costs, and achieves less amount of lye, less production, and lower alkalinity. The effect of liquid consumption
- Summary
- Abstract
- Description
- Claims
- Application Information
AI Technical Summary
Problems solved by technology
Method used
Examples
Embodiment 1
[0026] According to the volume mass ratio of water and nickel-cobalt lithium manganese oxide positive electrode material is 2mL / g, add water to the positive electrode material to adjust slurry to obtain slurry, then add 30wt% to the slurry according to the volume mass ratio of hydrogen peroxide and positive electrode material is 4mL / g Hydrogen peroxide is pre-reduced at 20°C for 4 hours, and then 0.6mol / L of dilute sulfuric acid is added at a rate of 2% of the amount of lithium in the positive electrode material according to the molar addition of dilute acid per minute, at a temperature of 85°C Under the condition of leaching for 3h, control the H in dilute sulfuric acid + The ratio of lithium to nickel-cobalt lithium manganate cathode material is 1.0:1.0. After leaching, the primary leachate and primary nickel-cobalt-manganese slag are obtained by filtration. The leaching rates of lithium, nickel, cobalt, and manganese in the primary leachate are respectively 92.51%. , 4.54%,...
Embodiment 2
[0028] According to the volume mass ratio of water and nickel-cobalt lithium manganese oxide positive electrode material is 2mL / g, the positive electrode material is mixed with water to obtain a slurry, and then according to the volume mass ratio of hydrogen peroxide and positive electrode material is 6mL / g, add 30wt% to the slurry Hydrogen peroxide is pre-reduced at 20°C for 4 hours, and then 0.6mol / L of dilute sulfuric acid is added at a rate of 1.5% of the amount of lithium in the positive electrode material according to the molar addition of dilute acid per minute. Under the condition of leaching for 3h, control the H in dilute sulfuric acid + The ratio of lithium to nickel-cobalt lithium manganate cathode material is 1.0:1.0. After leaching, the primary leachate and primary nickel-cobalt-manganese slag are obtained by filtration. The leaching rates of lithium, nickel, cobalt, and manganese in the primary leachate are 94.83% respectively. , 3.12%, 0.28%, 0.03%, and the pH ...
Embodiment 3
[0030] According to the volume mass ratio of water and nickel-cobalt lithium manganese oxide positive electrode material is 2mL / g, the positive electrode material is mixed with water to obtain a slurry, and then according to the volume mass ratio of hydrogen peroxide and positive electrode material is 6mL / g, add 30wt% to the slurry Hydrogen peroxide, pre-reduction at 20°C for 4h, and then adding 0.6mol / L dilute sulfuric acid at a rate of 1% of the amount of lithium in the positive electrode material as the molar addition of dilute acid per minute, at a temperature of 85°C Under leaching for 4 hours, control the H in dilute sulfuric acid + The ratio of lithium to nickel-cobalt lithium manganate cathode material is 1.3:1.0. After leaching, the primary leachate and primary nickel-cobalt-manganese slag are obtained by filtration. The leaching rates of lithium, nickel, cobalt, and manganese in the primary leachate are respectively 96.32%. , 20.51%, 0.73%, 0.06%, and the pH of the p...
PUM
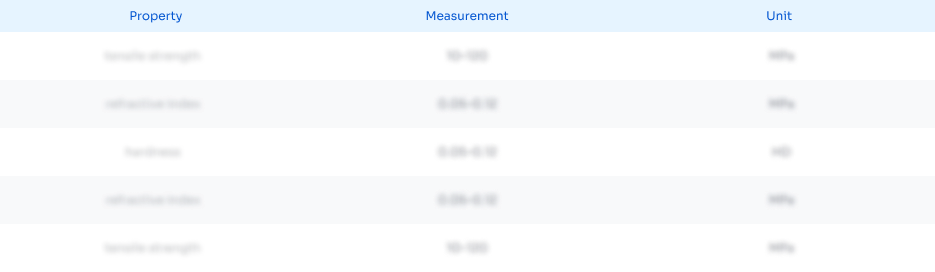
Abstract
Description
Claims
Application Information

- R&D
- Intellectual Property
- Life Sciences
- Materials
- Tech Scout
- Unparalleled Data Quality
- Higher Quality Content
- 60% Fewer Hallucinations
Browse by: Latest US Patents, China's latest patents, Technical Efficacy Thesaurus, Application Domain, Technology Topic, Popular Technical Reports.
© 2025 PatSnap. All rights reserved.Legal|Privacy policy|Modern Slavery Act Transparency Statement|Sitemap|About US| Contact US: help@patsnap.com