Multi-operation-mode piezoelectric viscosity sensor chip and working method and preparation method thereof
A sensor chip, multi-operation technology, applied in the field of MEMS sensors, can solve the problems of reducing the quality factor of the resonator, reducing the vibration stability of the resonator, weak damping resistance of the resonator, etc., to increase the fluid damping resistance and quality factor, Solve the effect of narrow viscosity measurement range and improve viscosity measurement sensitivity
- Summary
- Abstract
- Description
- Claims
- Application Information
AI Technical Summary
Problems solved by technology
Method used
Image
Examples
Embodiment Construction
[0039] The preferred implementation of the present invention will be further described in detail below in conjunction with the accompanying drawings and through examples.
[0040] Such as figure 1 and figure 2 As shown, the multi-operation mode piezoelectric viscosity sensor chip of the present invention includes a silicon substrate 5 and a silicon micro-cantilever resonator; the silicon micro-cantilever resonator includes a micro-cantilever suspension structure 1, a fixed support beam structure 6, a piezoresistive Beam structure and piezoresistive connection beam structure;
[0041] The piezoresistive beam structure includes a first piezoresistive beam 2-1, a second piezoresistive beam 2-2, a third piezoresistive beam 2-3, and a fourth piezoresistive beam 2-4; The connecting beam 9-1 and the second piezoresistive connecting beam 9-2; the piezoresistive beam and the piezoresistive connecting beam are arranged on both sides of the fixed support beam, wherein the first piezor...
PUM
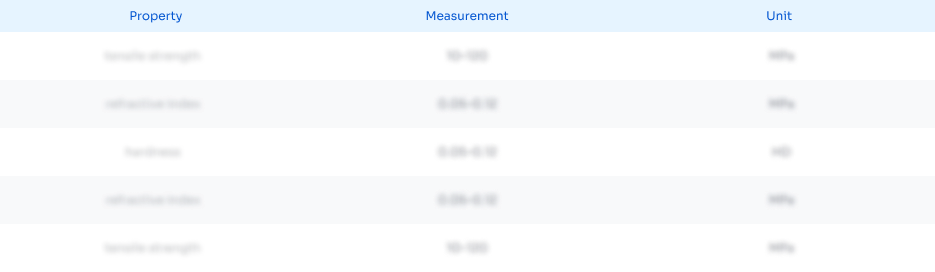
Abstract
Description
Claims
Application Information

- R&D Engineer
- R&D Manager
- IP Professional
- Industry Leading Data Capabilities
- Powerful AI technology
- Patent DNA Extraction
Browse by: Latest US Patents, China's latest patents, Technical Efficacy Thesaurus, Application Domain, Technology Topic, Popular Technical Reports.
© 2024 PatSnap. All rights reserved.Legal|Privacy policy|Modern Slavery Act Transparency Statement|Sitemap|About US| Contact US: help@patsnap.com