Active vision non-contact type servomechanism parameter measurement method and apparatus thereof
A servo-mechanism, non-contact technology, applied in the field of computer vision, can solve problems such as inability to apply accurate measurement, and achieve the effect of eliminating smearing, reducing difficulty, and simplifying processing
- Summary
- Abstract
- Description
- Claims
- Application Information
AI Technical Summary
Problems solved by technology
Method used
Image
Examples
Embodiment Construction
[0094] See figure 1 , figure 2 , image 3 , Figure 4 , Figure 5 , Figure 6 , Figure 7 As shown, its specific implementation is as follows:
[0095] (1) An active visual non-contact servomechanism parameter measurement device, which is composed of a measurement screen 1, a servomechanism installation platform 2, an image acquisition and processing system, and a red laser light source 3: a red laser light source is installed on the servomechanism 4 to be tested. Optical laser light source 3, which is placed on the servo mechanism installation platform 2 and placed in front of the measurement screen 1, a digital camera 5 is placed behind the servo mechanism 4 to be measured to image the measurement screen 1, and the image data is transmitted to the computer through the image acquisition card 7 System 6 processing.
[0096] The image acquisition and processing system is composed of a high-resolution digital camera 5, a computer system 6 and image measurement software....
PUM
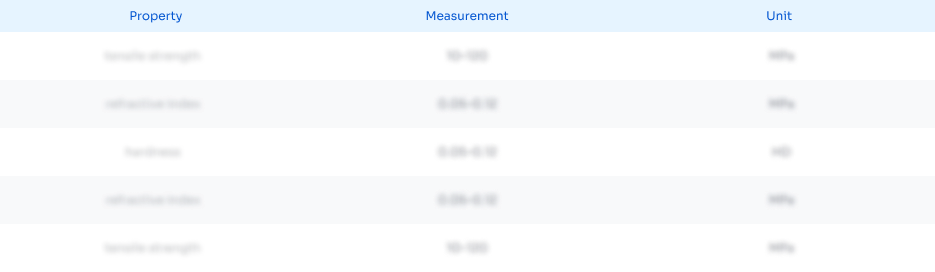
Abstract
Description
Claims
Application Information

- R&D
- Intellectual Property
- Life Sciences
- Materials
- Tech Scout
- Unparalleled Data Quality
- Higher Quality Content
- 60% Fewer Hallucinations
Browse by: Latest US Patents, China's latest patents, Technical Efficacy Thesaurus, Application Domain, Technology Topic, Popular Technical Reports.
© 2025 PatSnap. All rights reserved.Legal|Privacy policy|Modern Slavery Act Transparency Statement|Sitemap|About US| Contact US: help@patsnap.com