Durable anti-felting finishing method for wool fabric
An anti-felting and fabric technology, applied in the field of fabric fabrics, can solve the problems of shedding of the chitosan layer on the surface of wool fibers and the decline of the anti-felting performance of wool fabrics, so as to improve the anti-felting performance, improve the washing resistance and Durable anti-felting performance and the effect of improving anti-felting performance
- Summary
- Abstract
- Description
- Claims
- Application Information
AI Technical Summary
Problems solved by technology
Method used
Image
Examples
Embodiment 1
[0026] The long-lasting anti-felting finishing method for wool fabrics comprises the following steps:
[0027] 1) The wool fabric is placed in a plasma treatment apparatus for plasma pretreatment to obtain wool fabric a; wherein the plasma treatment conditions are: vacuum degree 35Pa, discharge time 3min, discharge power 50W;
[0028]2) Add tetrabutyl titanate to absolute ethanol and stir to prepare a tetrabutyl titanate solution with a concentration of 4%, and set aside; mix deionized water and absolute ethanol at a volume ratio of 1:3, and then add dropwise Adjust the pH to 3 with acetic acid to obtain a mixed solution for later use; put the wool fabric a into the tetrabutyl titanate solution at a bath ratio of 1:30, and then use the volume ratio of the mixed solution to the tetrabutyl titanate solution at a ratio of 1:2 , adding the mixed solution dropwise into the tetrabutyl titanate solution, standing still for 5 hours, placing the woolen fabric in an oven at 50° C. for 2...
Embodiment 2
[0034] The long-lasting anti-felting finishing method for wool fabrics comprises the following steps:
[0035] 1) The wool fabric is placed in a plasma treatment apparatus for plasma pretreatment to obtain wool fabric a; wherein the plasma treatment conditions are: vacuum degree 20Pa, discharge time 1min, discharge power 100W;
[0036] 2) Add tetrabutyl titanate to absolute ethanol and stir to prepare a tetrabutyl titanate solution with a concentration of 2%, and set aside; mix deionized water and absolute ethanol at a volume ratio of 1:3, and then add dropwise Adjust the pH to 2 with acetic acid to obtain a mixed solution for later use; put the wool fabric a into the tetrabutyl titanate solution at a bath ratio of 1:30, and then use the ratio of the mixed solution to the tetrabutyl titanate solution at a volume ratio of 1:2 , adding the mixed solution dropwise into the tetrabutyl titanate solution, standing still for 4 hours, placing the woolen fabric in an oven at 50° C. for...
Embodiment 3
[0042] The long-lasting anti-felting finishing method for wool fabrics comprises the following steps:
[0043] 1) The wool fabric is placed in a plasma treatment apparatus for plasma pretreatment to obtain wool fabric a; wherein the plasma treatment conditions are: vacuum degree 30Pa, discharge time 2min, discharge power 80W;
[0044] 2) Add tetrabutyl titanate to absolute ethanol and stir to prepare a tetrabutyl titanate solution with a concentration of 5%, and set aside; mix deionized water and absolute ethanol at a volume ratio of 1:3, and then add dropwise Adjust the pH to 2.5 with acetic acid to obtain a mixed solution for later use; put the wool fabric a into the tetrabutyl titanate solution at a bath ratio of 1:30, and then use the ratio of the mixed solution to the tetrabutyl titanate solution at a volume ratio of 1:2 , adding the mixed solution dropwise into the tetrabutyl titanate solution, standing still for 6 hours, placing the woolen fabric in an oven at 50° C. fo...
PUM
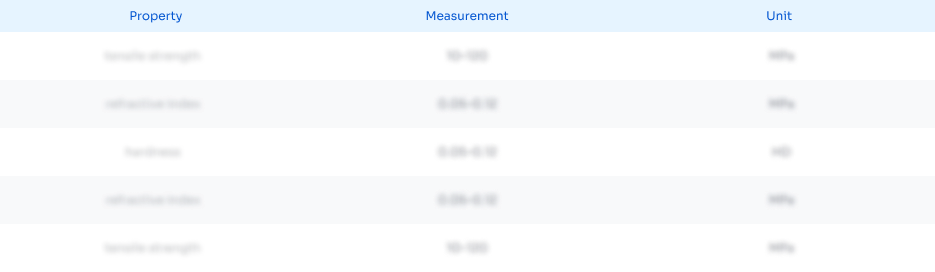
Abstract
Description
Claims
Application Information

- R&D
- Intellectual Property
- Life Sciences
- Materials
- Tech Scout
- Unparalleled Data Quality
- Higher Quality Content
- 60% Fewer Hallucinations
Browse by: Latest US Patents, China's latest patents, Technical Efficacy Thesaurus, Application Domain, Technology Topic, Popular Technical Reports.
© 2025 PatSnap. All rights reserved.Legal|Privacy policy|Modern Slavery Act Transparency Statement|Sitemap|About US| Contact US: help@patsnap.com