Synthesis method of polyvinyl butyral resin
A technology of polyvinyl butyral resin and synthesis method, which is applied in the field of polymer materials, can solve problems such as uneven precipitation of resin, uneven degree of acetalization, and difficulty in post-processing, so as to improve reaction conversion rate and operability Strong, easy to industrialize the effect of production
- Summary
- Abstract
- Description
- Claims
- Application Information
AI Technical Summary
Problems solved by technology
Method used
Examples
Embodiment 1
[0028](1) Add 1,000 parts of deionized water and 90 parts of PVA1799 polyvinyl alcohol into a reactor equipped with electric stirring, temperature control and reflux condensing device, stir and heat up to 90°C until the polyvinyl alcohol is completely dissolved to form a uniform solution ;
[0029] (2) Adjust the temperature of the reaction system to 40°C, add 0.5 parts of emulsifier sodium dodecylsulfonate, and stir until a uniform solution is formed;
[0030] (3) Keep the temperature of the reaction system at 40°C, add 55 parts of n-butyraldehyde and 12 parts of oxalic acid mixture, and keep the temperature at 40°C for 3 hours;
[0031] (4) Keep the temperature of the reaction system at 40°C, add 6 parts of 30% hydrochloric acid by mass percent, gradually increase the temperature of the reaction system to 70°C within 0.5 hours, and keep the temperature at 70°C for 4 hours;
[0032] (5) Regulating the temperature of the reaction system to 30° C., adding a mass percent concen...
Embodiment 2
[0035] (1) Add 1,000 parts of deionized water and 100 parts of PVA1799 polyvinyl alcohol into a reactor equipped with electric stirring, temperature control and reflux condensing device, stir and heat up to 95°C until the polyvinyl alcohol is completely dissolved to form a uniform solution ;
[0036] (2) Adjust the temperature of the reaction system to 30°C, add 1.5 parts of emulsifier sodium lauryl sulfate, and stir until a uniform solution is formed;
[0037] (3) Keep the reaction system temperature at 30°C, add 65 parts of n-butyraldehyde and 6 parts of formic acid mixture, keep the temperature at 40°C for 3 hours;
[0038] (4) Keep the temperature of the reaction system at 30°C, add 15 parts by mass of 30% hydrochloric acid, gradually increase the temperature of the reaction system to 65°C within 0.5 hours, and keep the temperature at 65°C for 3 hours;
[0039] (5) Regulating the temperature of the reaction system to 30° C., adding a mass percent concentration of 3% potas...
Embodiment 3
[0042] (1) Add 1,000 parts of deionized water and 110 parts of PVA1799 polyvinyl alcohol into a reactor equipped with electric stirring, temperature control and reflux condensing device, stir and heat up to 90°C until the polyvinyl alcohol is completely dissolved to form a uniform solution ;
[0043] (2) Adjust the temperature of the reaction system to 40°C, add 0.5 parts of emulsifier sodium dodecylbenzenesulfonate, and stir until a uniform solution is formed;
[0044] (3) Keep the temperature of the reaction system at 40°C, add 80 parts of n-butyraldehyde and 15 parts of maleic acid mixture, and keep the temperature at 40°C for 3 hours;
[0045] (4) Keep the temperature of the reaction system at 40°C, add 8 parts of 30% sulfuric acid by mass percentage, gradually increase the temperature of the reaction system to 70°C within 0.5 hours, and keep the temperature at 70°C for 3 hours;
[0046] (5) Regulating the temperature of the reaction system to 30° C., adding a mass percen...
PUM
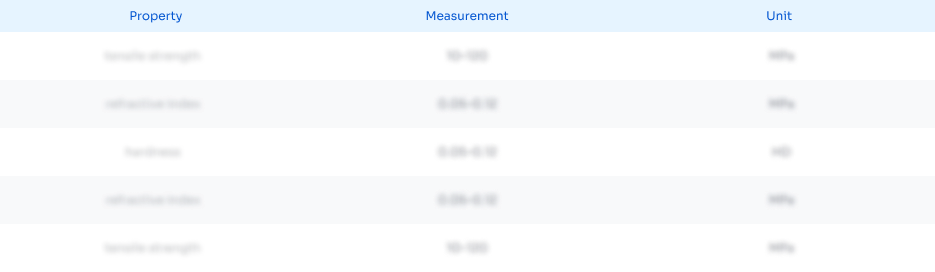
Abstract
Description
Claims
Application Information

- Generate Ideas
- Intellectual Property
- Life Sciences
- Materials
- Tech Scout
- Unparalleled Data Quality
- Higher Quality Content
- 60% Fewer Hallucinations
Browse by: Latest US Patents, China's latest patents, Technical Efficacy Thesaurus, Application Domain, Technology Topic, Popular Technical Reports.
© 2025 PatSnap. All rights reserved.Legal|Privacy policy|Modern Slavery Act Transparency Statement|Sitemap|About US| Contact US: help@patsnap.com