Wet-process tower for deacidification by wet process
A wet method and deacidification technology, applied in separation methods, chemical instruments and methods, gas treatment, etc., can solve the problems of equipment aging, affecting the service life and use effect of equipment, so as to maintain integrity, reduce water vapor and effective Effect of acid gas content, resistance to decomposition and deformation
- Summary
- Abstract
- Description
- Claims
- Application Information
AI Technical Summary
Problems solved by technology
Method used
Image
Examples
Embodiment 1
[0033] Preparation of PP filler layer The filler is prepared from the following raw materials in parts by weight: 100 parts of polypropylene, 20 parts of glass fiber, 15 parts of mineral filler, 30 parts of compatibilizer, 0.5 part of lubricant, and 0.75 part of antioxidant.
[0034] The preparation method of the filler is as follows:
[0035] Step 1. Weighing raw materials according to the proportion for later use, wherein the polypropylene and mineral fillers are dried to obtain a dry mixture for later use;
[0036] Step 2. Add the mixture A of step 1, maleic anhydride graft, compatibilizer, lubricant and antioxidant into the high-speed mixer in sequence, use the high-speed mixer to mix the materials for 10 minutes, and then add the mixed materials into the double In the screw extruder, glass fiber is added to the exhaust port of the twin-screw extruder at the same time as melting and extruding, and it is melted and reacted to extrude and granulate.
[0037] The process con...
Embodiment 2
[0039] Preparation of PP filler layer The filler is prepared from the following raw materials in parts by weight: 100 parts of polypropylene, 25 parts of glass fiber, 17.5 parts of mineral filler, 25 parts of compatibilizer, 0.75 part of lubricant, and 1 part of antioxidant.
[0040] The preparation method of the filler is as follows:
[0041] Step 1. Weighing raw materials according to the proportion for later use, wherein the polypropylene and mineral fillers are dried to obtain a dry mixture for later use;
[0042] Step 2. Add the mixture A of step 1, maleic anhydride graft, compatibilizer, lubricant and antioxidant into the high-speed mixer in sequence, use the high-speed mixer to mix the materials for 10 minutes, and then add the mixed materials into the double In the screw extruder, glass fiber is added to the exhaust port of the twin-screw extruder at the same time as melting and extruding, and it is melted and reacted to extrude and granulate.
[0043] The process con...
Embodiment 3
[0045] Preparation of PP filler layer The filler is prepared from the following raw materials in parts by weight: 100 parts of polypropylene, 30 parts of glass fiber, 25 parts of mineral filler, 30 parts of compatibilizer, 1 part of lubricant, and 1.25 parts of antioxidant.
[0046] The preparation method of the filler is as follows:
[0047] Step 1. Weighing raw materials according to the proportion for later use, wherein the polypropylene and mineral fillers are dried to obtain a dry mixture for later use;
[0048] Step 2. Add the mixture A of step 1, maleic anhydride graft, compatibilizer, lubricant and antioxidant into the high-speed mixer in sequence, use the high-speed mixer to mix the materials for 10 minutes, and then add the mixed materials into the double In the screw extruder, glass fiber is added to the exhaust port of the twin-screw extruder at the same time as melting and extruding, and it is melted and reacted to extrude and granulate.
[0049] The process cond...
PUM
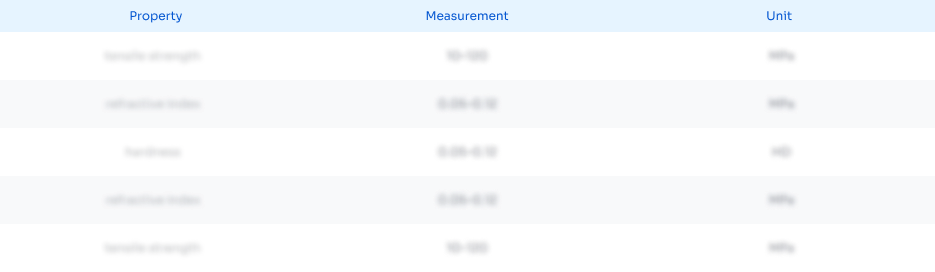
Abstract
Description
Claims
Application Information

- R&D
- Intellectual Property
- Life Sciences
- Materials
- Tech Scout
- Unparalleled Data Quality
- Higher Quality Content
- 60% Fewer Hallucinations
Browse by: Latest US Patents, China's latest patents, Technical Efficacy Thesaurus, Application Domain, Technology Topic, Popular Technical Reports.
© 2025 PatSnap. All rights reserved.Legal|Privacy policy|Modern Slavery Act Transparency Statement|Sitemap|About US| Contact US: help@patsnap.com