A kind of calcium silicate board and preparation method thereof
A calcium silicate board and silicon dioxide technology, applied in the field of building materials, can solve the problems of poor temperature resistance, easy cracks, and high water absorption of calcium silicate boards, and achieve easy operation, reduced crack rate, and low production costs. Effect
- Summary
- Abstract
- Description
- Claims
- Application Information
AI Technical Summary
Problems solved by technology
Method used
Examples
Embodiment 1
[0031] A kind of calcium silicate board of the present embodiment, comprises following raw material to make: quartz sand 47kg, cement 15kg, fly ash 12kg, superfine ceramic fiber 15kg, paper fiber 3kg;
[0032] Wherein, the fly ash includes the following raw materials in parts by weight: 24 parts of silicon dioxide, 25 parts of aluminum oxide, 10 parts of calcium oxide, 2 parts of magnesium oxide, 5.6 parts of ferric oxide, and the paper fiber It is obtained by adding pulp debonding agent to the pulp board and dissolving it for 20 minutes.
[0033] The preparation method of the calcium silicate board of the present embodiment may further comprise the steps:
[0034] (1) take by weighing according to the parts by weight of each raw material for subsequent use;
[0035] (2) Mix cement and fly ash with water and mix evenly. The mass ratio of cement and fly ash to water is 2:7 to obtain a mixed slurry. Add quartz sand to the mixed slurry and stir evenly, and then add Stir until t...
Embodiment 2
[0040] A kind of calcium silicate board of the present embodiment, comprises following raw material to make: quartz sand 48.5kg, cement 16.5kg, fly ash 14kg, superfine ceramic fiber 16.5kg, paper fiber 5kg;
[0041] Wherein, the fly ash includes the following raw materials in parts by weight: 26.02 parts of silicon dioxide, 26.64 parts of aluminum oxide, 11.75 parts of calcium oxide, 2.27 parts of magnesium oxide, 5.88 parts of ferric oxide, and the paper fiber It is obtained by adding pulp debonding agent to the pulp board and dissolving it for 25 minutes.
[0042] The preparation method of the calcium silicate board of the present embodiment may further comprise the steps:
[0043] (1) take by weighing according to the parts by weight of each raw material for subsequent use;
[0044] (2) Mix cement and fly ash with water and mix evenly. The mass ratio of cement and fly ash to water is 3:7 to obtain a mixed slurry. Add quartz sand to the mixed slurry and stir evenly, and the...
Embodiment 3
[0049] A kind of calcium silicate board of the present embodiment, comprises following raw material to make: quartz sand 50kg, cement 18kg, fly ash 16kg, superfine ceramic fiber 18kg, paper fiber 7kg;
[0050] Wherein, the fly ash includes the following raw materials in parts by weight: 28 parts of silicon dioxide, 28 parts of aluminum oxide, 14 parts of calcium oxide, 2.5 parts of magnesium oxide, 6.0 parts of ferric oxide, and the paper fiber It is obtained by adding pulp debonding agent to the pulp board and dissolving it for 30 minutes.
[0051] The preparation method of the calcium silicate board of the present embodiment may further comprise the steps:
[0052] (1) take by weighing according to the parts by weight of each raw material for subsequent use;
[0053] (2) Cement and fly ash are mixed with water and stirred evenly, the mass ratio of cement and fly ash to water is 4:7 to obtain a mixed slurry, quartz sand is added to the mixed slurry and stirred evenly, and th...
PUM
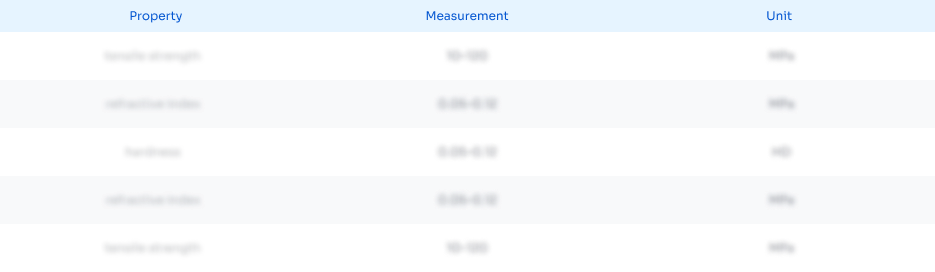
Abstract
Description
Claims
Application Information

- R&D
- Intellectual Property
- Life Sciences
- Materials
- Tech Scout
- Unparalleled Data Quality
- Higher Quality Content
- 60% Fewer Hallucinations
Browse by: Latest US Patents, China's latest patents, Technical Efficacy Thesaurus, Application Domain, Technology Topic, Popular Technical Reports.
© 2025 PatSnap. All rights reserved.Legal|Privacy policy|Modern Slavery Act Transparency Statement|Sitemap|About US| Contact US: help@patsnap.com