Antistatic fabric preparation method
An antistatic and fabric technology, applied in the direction of textile, fabric, fiber type, etc., can solve the problems that cannot be achieved, the antistatic treatment agent on the surface of the fabric falls off, and cannot be used for a long time
- Summary
- Abstract
- Description
- Claims
- Application Information
AI Technical Summary
Problems solved by technology
Method used
Image
Examples
Embodiment 1
[0028] S1. Selection of raw materials: firstly select clean reel polyester filament, stainless steel fiber, carbon black conductive fiber and anti-static synthetic fiber. The carbon black conductive fiber is carbonized polyacrylonitrile fiber, carbonized cellulose fiber and carbonized pitch system. The anti-static synthetic fiber is a synthetic fiber prepared by mixing high-concentration titanium dioxide conductive particles into antimony oxide fibers containing tin oxide by using a composite spinning method;
[0029] S2. Preparation of treatment liquid: Pour 7L of antistatic mixture into the soaking tank, then add 2.5L of clear water, and stir for 25min at a speed of 250r / min with a stirring device to fully mix the antistatic mixture with clean water. The raw materials of the antistatic mixture include: 45 parts by weight of quaternary ammonium salt, 7 parts of sulfate ester, 7 parts of phosphate ester, 7 parts of dispersant, 7 parts of cationic surfactant and 7 parts of viscous ...
Embodiment 2
[0034] S1. Selection of raw materials: firstly select clean reel polyester filament, stainless steel fiber, carbon black conductive fiber and anti-static synthetic fiber. The carbon black conductive fiber is woven from carbonized polyacrylonitrile fiber and carbonized cellulose fiber. Anti-static synthetic fiber is a synthetic fiber prepared by mixing high-concentration titanium dioxide conductive particles into antimony oxide fibers containing tin oxide by a composite spinning method;
[0035] S2. Preparation of treatment liquid: Pour 5L of antistatic mixture into the soaking tank, then add 2L of clear water, and stir for 20min at a speed of 200r / min through a stirring device, so that the antistatic mixture and clear water can be fully prepared. The raw materials of the electrostatic mixing liquid include: 40 parts of quaternary ammonium salt, 5 parts of sulfuric acid ester, 5 parts of phosphate ester, 5 parts of dispersant, 5 parts of cationic surfactant and 5 parts of viscous a...
Embodiment 3
[0040] S1. Selection of raw materials: firstly select clean reel polyester filament, stainless steel fiber, carbon black conductive fiber and anti-static synthetic fiber. The carbon black conductive fiber is woven from carbonized cellulose fiber and carbonized pitch-based fiber. Electrostatic synthetic fiber is a synthetic fiber made by locally mixing high-concentration titanium dioxide conductive particles into antimony oxide fibers containing tin oxide using a composite spinning method;
[0041] S2. Preparation of treatment liquid: Pour 10L of antistatic mixture into the soaking tank, then add 3L of clear water, and stir for 30min at 300r / min with a stirring device to make the antistatic mixture and clear water be fully prepared. The raw materials of the electrostatic mixture include 50 parts by weight of quaternary ammonium salt, 10 parts of sulfate ester, 10 parts of phosphate ester, 10 parts of dispersant, 10 parts of cationic surfactant and 10 parts of viscous agent. The dis...
PUM
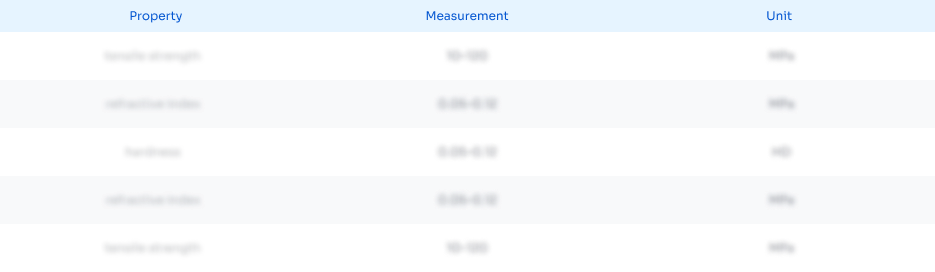
Abstract
Description
Claims
Application Information

- R&D
- Intellectual Property
- Life Sciences
- Materials
- Tech Scout
- Unparalleled Data Quality
- Higher Quality Content
- 60% Fewer Hallucinations
Browse by: Latest US Patents, China's latest patents, Technical Efficacy Thesaurus, Application Domain, Technology Topic, Popular Technical Reports.
© 2025 PatSnap. All rights reserved.Legal|Privacy policy|Modern Slavery Act Transparency Statement|Sitemap|About US| Contact US: help@patsnap.com