Semi-aromatic nylon modified composite material and preparation method thereof
The technology of semi-aromatic nylon and composite material is applied in the field of semi-aromatic nylon modified composite material and its preparation, which can solve the problems of restricting the application of high-temperature resistant nylon, difficult plastic processing equipment processing, expensive nylon and the like, and achieves cohesion. Can reduce, reduce melt viscosity, improve the effect of comprehensive performance
- Summary
- Abstract
- Description
- Claims
- Application Information
AI Technical Summary
Problems solved by technology
Method used
Image
Examples
preparation example Construction
[0026] A method for preparing a semi-aromatic nylon modified composite material, specifically: mixing the dried semi-aromatic nylon resin, lithium halide, and additives according to the required ratio, and then discharging them into a parallel twin-screw extruder for melt blending and extruding It can be granulated.
[0027] The raw material composition of the composite material also includes silane-modified calcium sulfate whiskers, the weight ratio of which to semi-aromatic nylon resin is 15-25:80-100, and the silane-modified calcium sulfate whiskers are prepared according to the following method get:
[0028] The anhydrous dead-burned calcium sulfate whisker, the crystal form modifier and the surface modifier are mixed, followed by washing, filtering and drying in sequence to obtain the silane-modified calcium sulfate whisker.
[0029] In the preparation method of the composite material, the extrusion process temperature of the twin-screw extruder is: 250±5°C in the first ...
Embodiment 1
[0048] A semi-aromatic nylon modified composite material, its raw material composition and weight ratio are: semi-aromatic nylon resin PA4T 80, lithium bromide 2, silane-modified calcium sulfate whisker 15, polytetrafluoroethylene micropowder 1, cyclic poly Ester 3, antioxidant 10760.3, antioxidant 168 0.3, wherein, the raw material composition and weight ratio of the silane-modified calcium sulfate whisker are: anhydrous dead-burned calcium sulfate whisker 80, dodecyl Trimethoxysilane 1, lithium chloride 2, liquid paraffin 1.
[0049] The above-mentioned composite material is prepared according to the following steps in turn:
[0050] Step 1. First add anhydrous dead-burned calcium sulfate whiskers and lithium chloride into the mixer according to the required ratio, set the temperature of the mixer at 105°C, stir at 950 rpm, and then add liquid paraffin The diluted dodecyltrimethoxysilane was stirred for 15 minutes, then the mixture was taken out, washed with water, filtered...
Embodiment 2
[0053] The difference with Example 1 is:
[0054] The raw material composition and weight ratio of the composite material are: semi-aromatic nylon resin PA4T 100, lithium bromide 3, silane-modified calcium sulfate whisker 25, polytetrafluoroethylene micropowder 2, cyclic polyester 5, antioxidant 1076 0.5. Antioxidant 168 0.5, wherein the raw material composition and weight ratio of the silane-modified calcium sulfate whiskers are: anhydrous dead-burned calcium sulfate whiskers 100, dodecyltrimethoxysilane 3, Lithium chloride 4, liquid paraffin 3.
PUM
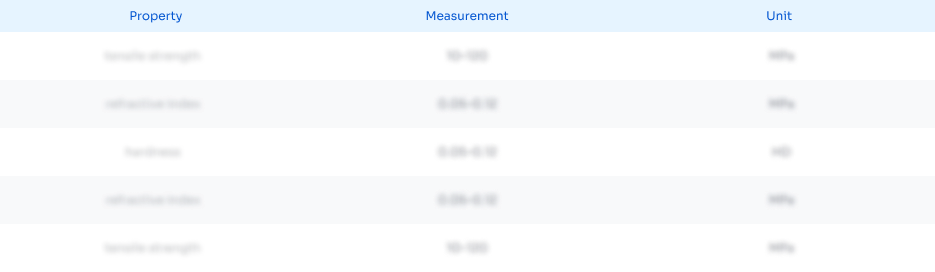
Abstract
Description
Claims
Application Information

- R&D
- Intellectual Property
- Life Sciences
- Materials
- Tech Scout
- Unparalleled Data Quality
- Higher Quality Content
- 60% Fewer Hallucinations
Browse by: Latest US Patents, China's latest patents, Technical Efficacy Thesaurus, Application Domain, Technology Topic, Popular Technical Reports.
© 2025 PatSnap. All rights reserved.Legal|Privacy policy|Modern Slavery Act Transparency Statement|Sitemap|About US| Contact US: help@patsnap.com