Strong-support high-elasticity polyurethane flexible foam material and preparation method thereof
A technology of polyurethane soft foam and high elasticity, which is applied in the field of polyurethane soft foam material, strong support and high elasticity polyurethane soft foam material and its preparation, and can solve problems such as difficult balance, contradiction between softness and support
- Summary
- Abstract
- Description
- Claims
- Application Information
AI Technical Summary
Problems solved by technology
Method used
Image
Examples
Embodiment 1
[0033] Example 1 Preparation of Lignin-Based Block Copolymer Molecular-Level Combined Polyether
[0034] A method for preparing lignin-based block copolymerized molecular-level combined polyether, the process flow diagram is shown in figure 1 , the method includes the following steps:
[0035] 1) Pretreatment of lignosulfonate:
[0036] Lignosulfonate and pretreatment reagent are mixed in a weight ratio of 1:2-10, and pretreated for 60-240 minutes at a temperature of 100-140°C and a pressure of 10-15MPa;
[0037] 2) Remove the pretreatment reagent:
[0038] The lignosulfonate obtained after the pretreatment is sloughed off the pretreatment reagent through vacuum distillation;
[0039] 3) Soft and hard copolymerization of lignosulfonate and polyether polyol:
[0040] Lignosulfonate and polyether polyols are copolymerized at a weight ratio of 1:1-5, the copolymerization temperature is 120-180°C, and the time is 1-4 hours. After the reaction is completed, a lignin-based block...
Embodiment 8-10
[0057] A method for preparing a strongly supported and highly elastic flexible polyurethane foam material. The method uses the lignin-based block copolymerized molecular-level combined polyether prepared in Example 7 as a raw material. The raw material formula of the polyurethane flexible foam is shown in Table 3.
[0058] Table 3 (unit kg)
[0059]
[0060] The above-mentioned raw materials are mixed and stirred evenly in a high-speed mixer, and foamed at a material temperature of 15-25 degrees Celsius to obtain soft polyurethane foam. After testing, the technical indicators of the polyurethane soft foam are shown in Table 4. The one-dimensional density function curve of polyurethane foam is shown in figure 2 , according to the structure diagram of lignin-based polyurethane foam inferred from the SAXS map, see image 3 .
[0061] Table 4
[0062]
[0063] The data in Table 4 proves that compared with the standard sample, the polyurethane soft foam adopting lignin-b...
PUM
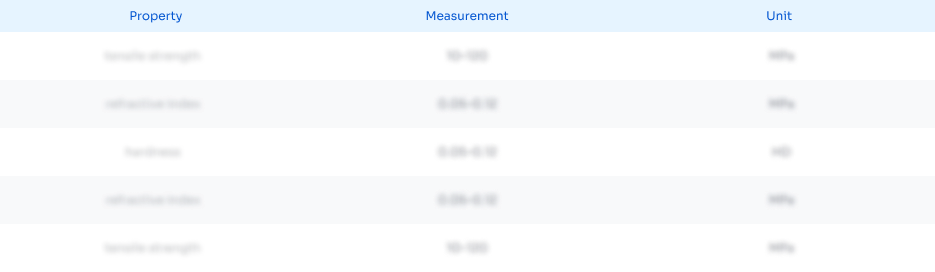
Abstract
Description
Claims
Application Information

- Generate Ideas
- Intellectual Property
- Life Sciences
- Materials
- Tech Scout
- Unparalleled Data Quality
- Higher Quality Content
- 60% Fewer Hallucinations
Browse by: Latest US Patents, China's latest patents, Technical Efficacy Thesaurus, Application Domain, Technology Topic, Popular Technical Reports.
© 2025 PatSnap. All rights reserved.Legal|Privacy policy|Modern Slavery Act Transparency Statement|Sitemap|About US| Contact US: help@patsnap.com