Large-gap argon arc welding bottom sealing repair method for carbon steel pipeline and container
A technology of argon arc welding and large gap, which is applied in the direction of arc welding equipment, welding equipment, workpiece edge, etc., which can solve the problems of enlarged root gap, large volume, wide molten pool, etc., and achieve the reduction of stress concentration and mechanical properties Good, less prone to cracking effect
- Summary
- Abstract
- Description
- Claims
- Application Information
AI Technical Summary
Problems solved by technology
Method used
Image
Examples
Embodiment Construction
[0024] Further description will be given below in conjunction with the embodiments of the accompanying drawings.
[0025] as the picture shows,
[0026] Step 1: Welding defect location: Determine the nature, depth, length, width and direction of pipeline defects (slag inclusions, lack of fusion, cracks, incomplete penetration, pores) through non-destructive testing, and locate and identify the appearance ,Record.
[0027] Step 2: Defect cleaning: According to the location, nature and size of the defect, choose the method of carbon arc gouging or cutting and grinding, digging from the outer surface of the pipeline from the outside to the inside, and observe in time as the thickness of the digging increases. , Measure until the defect location is found. For metals with a high tendency to be hardened, preheating is required during carbon arc gouging to prevent new defects.
[0028] Step 3: Groove grinding: After digging to the defect position, grind the groove shape so that th...
PUM
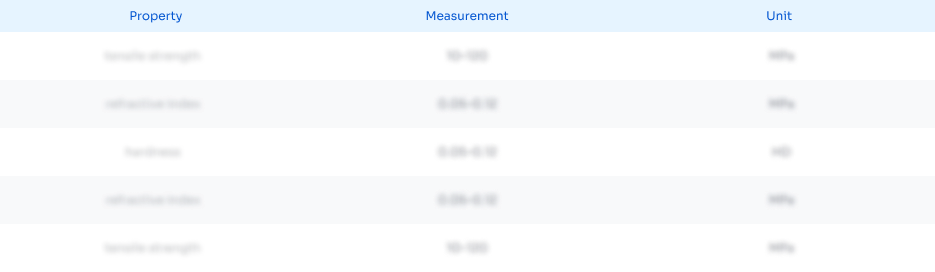
Abstract
Description
Claims
Application Information

- R&D
- Intellectual Property
- Life Sciences
- Materials
- Tech Scout
- Unparalleled Data Quality
- Higher Quality Content
- 60% Fewer Hallucinations
Browse by: Latest US Patents, China's latest patents, Technical Efficacy Thesaurus, Application Domain, Technology Topic, Popular Technical Reports.
© 2025 PatSnap. All rights reserved.Legal|Privacy policy|Modern Slavery Act Transparency Statement|Sitemap|About US| Contact US: help@patsnap.com