Modified carbon nitride/Fe-based MOF composite material and preparation method and application thereof
A composite material and carbon nitride technology, applied in the field of visible light catalysis, can solve the problems of poor photoresponsiveness, high band gap, and small specific surface area, and achieve the effects of convenient synthesis, easy recycling, and high photocatalytic activity
- Summary
- Abstract
- Description
- Claims
- Application Information
AI Technical Summary
Problems solved by technology
Method used
Image
Examples
Embodiment 1
[0026] NH containing different proportions of aminoterephthalic acid ligands 2-MIL-53(Fe)-X% preparation
[0027] 1) NH 2 -MIL-53(Fe)-100% (i.e. NH 2 - Preparation of MIL-53(Fe))
[0028] First, 2mmol FeCl 3 ·6H 2 O and 2mmol of aminoterephthalic acid were dissolved in 40mL of N,N-dimethylformamide, magnetically stirred for 60min, then transferred to a hydrothermal kettle, heated at 150°C for 15h, naturally cooled to room temperature, at a rate of 8000rpm, Centrifuge for 5min, then wash twice with DMF and methanol respectively, and finally dry in vacuum at 100°C for 12h to obtain the NH 2 -MIL-53(Fe)-100%.
[0029] 2) NH 2 - Preparation of MIL-53(Fe)-75%
[0030] First, 2mmol FeCl 3 ·6H 2 O, 1.5mmol aminoterephthalic acid and 0.5mmol terephthalic acid were dissolved in 40mL of N,N-dimethylformamide, stirred by magnetic force for 60min, then transferred to a hydrothermal kettle, heated at 150°C for 15h, and naturally Cool to room temperature, centrifuge at 8000rpm fo...
Embodiment 2
[0042] g-C 3 N 4 Preparation of -M dispersion liquid (stripping liquid)
[0043] 1) g-C 3 N 4 -M preparation
[0044] Weigh melamine and triaminopyrimidine and mix them uniformly in a molar ratio of 1:3, spread them on a quartz boat, heat them in a tube furnace under nitrogen atmosphere, and raise the temperature to 500 °C at a heating rate of 5 °C / min. ℃ for 120 min, and finally cooled to room temperature under nitrogen purging to obtain powdery g-C 3 N 4 -M, after being ground into powder, sonicated in pure DMSO for 120min to exfoliate g-C 3 N 4 -M particles, centrifuged five times with distilled water at 8000 rpm in a centrifuge, and then dried in a vacuum oven at 60°C for 12 hours and collected.
[0045] 2) g-C 3 N 4 -M dispersion preparation
[0046] Weigh the good g-C prepared in step 1) 3 N 4 -M particles 50 mg, added to DMF and ultrasonicated for half an hour to obtain g-C with a concentration of 1 mg / mL 3 N 4 -M dispersion.
Embodiment 3
[0048] Preparation of multiple composite catalysts
[0049] 1) g-C 3 N 4 -M / NH 2 - Preparation of MIL-53(Fe)-50%
[0050] First, 2mmol FeCl 3 ·6H 2 O, 1mmol of aminoterephthalic acid and 1mmol of terephthalic acid were dissolved in 40mL of N-N-dimethylformamide, and different volumes (0.5mL, 1.0mL, 1.5mL, 2mL) of g-C prepared in Example 2 were added 3 N 4 -M dispersion liquid, magnetically stirred for 60min, then transferred to a hydrothermal kettle, heated at 150°C for 15h, cooled to room temperature naturally, centrifuged at 8000rpm for 5min, then washed twice with DMF and methanol respectively, and finally washed at 100 Vacuum drying at ℃ for 12h to obtain g-C 3 N 4 -M g-C with different loading ratios 3 N 4 -M / NH 2 -MIL-53(Fe)-50%.
[0051] 2) Performance test of photocatalytic reduction of Cr(VI)
[0052] Take 10mg g-C 3 N 4 -M g-C with different loading ratios 3 N 4 -M / NH 2 -MIL-53(Fe)-50%, added to the potassium dichromate solution (100mL) with a Cr(VI...
PUM
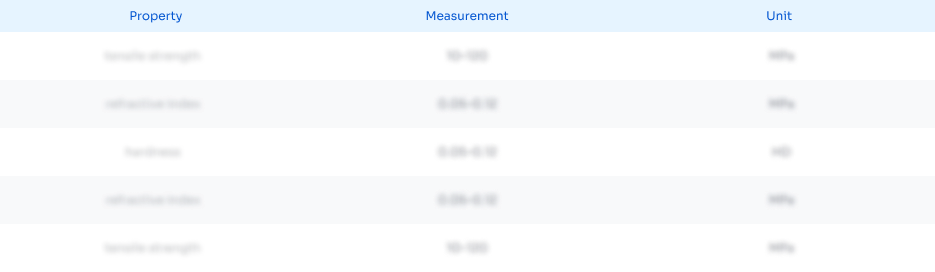
Abstract
Description
Claims
Application Information

- Generate Ideas
- Intellectual Property
- Life Sciences
- Materials
- Tech Scout
- Unparalleled Data Quality
- Higher Quality Content
- 60% Fewer Hallucinations
Browse by: Latest US Patents, China's latest patents, Technical Efficacy Thesaurus, Application Domain, Technology Topic, Popular Technical Reports.
© 2025 PatSnap. All rights reserved.Legal|Privacy policy|Modern Slavery Act Transparency Statement|Sitemap|About US| Contact US: help@patsnap.com