Laminated material hole-making machining track planning method
A technology of laminated materials and trajectory planning, applied in the direction of manufacturing tools, metal processing equipment, milling machine equipment details, etc., can solve the problems of reducing the revolution speed of the terminal hole-making actuator, no significant improvement in processing defects, and dividing processing stages. Achieve the effect of improving the overall processing quality, improving the overall hole making precision, reducing the hole diameter deviation and roundness
- Summary
- Abstract
- Description
- Claims
- Application Information
AI Technical Summary
Problems solved by technology
Method used
Image
Examples
Embodiment 1
[0050] Determine the thickness and aperture range of the workpiece material according to the composition of the laminated material: the double laminated material is composed of an upper layer of CFRP composite material and a lower layer of titanium alloy. The thickness of the titanium alloy material layer is 5-10mm, and the thickness of the CFRP composite material layer is titanium alloy. 2 times the layer thickness, the diameter of the machining hole is 10-20mm, and the ratio of the hole diameter to the tool diameter is 1.5.
[0051] Using traditional end mills, the spiral milling hole terminal actuator is used under the industrial robot platform to implement the hole-making processing of the double-layer laminated material. The spiral milling hole terminal actuator used in the present invention is an existing technology, which generally includes a tool Rotation unit, tool revolution unit, tool radial offset unit, axial feed unit, etc., can realize the control of various paramete...
Embodiment 2
[0062] According to the composition of the laminated material, determine the thickness of the workpiece material and the range of the pore diameter: the sandwich laminated material is composed of the upper layer of CFRP composite material, the middle layer of titanium alloy and the lower layer of CFRP composite material. Among them, the thickness of the titanium alloy material layer ranges from 5 to 7 mm, and the thickness of the CFRP composite material layer is twice the thickness of the titanium alloy layer. The diameter range of the machining hole is 15-30mm, and the ratio of the hole diameter to the tool diameter is 1.3.
[0063] Using traditional end mills, the spiral milling hole terminal actuator is used under the industrial numerical control machine tool platform to implement the hole-making processing of the sandwich laminated material. The spiral milling hole terminal actuator used in the present invention is an existing technology, which generally includes Tool rotatio...
PUM
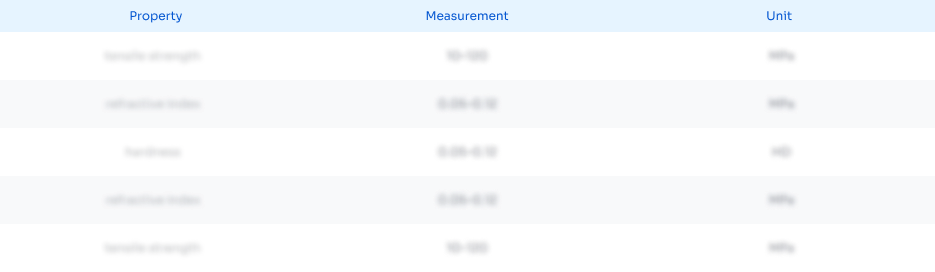
Abstract
Description
Claims
Application Information

- R&D
- Intellectual Property
- Life Sciences
- Materials
- Tech Scout
- Unparalleled Data Quality
- Higher Quality Content
- 60% Fewer Hallucinations
Browse by: Latest US Patents, China's latest patents, Technical Efficacy Thesaurus, Application Domain, Technology Topic, Popular Technical Reports.
© 2025 PatSnap. All rights reserved.Legal|Privacy policy|Modern Slavery Act Transparency Statement|Sitemap|About US| Contact US: help@patsnap.com