Preparation method of alpha-cellulose, spinning composition, and fiber material
A fiber material and cellulose technology, which is applied in the fields of cellulose raw material pulping, single-component cellulose rayon, fiber raw material processing, etc. question
- Summary
- Abstract
- Description
- Claims
- Application Information
AI Technical Summary
Problems solved by technology
Method used
Image
Examples
Embodiment 1
[0053] Add 100 parts by weight of dried coffee grounds (dried at 80° C. for 120 minutes), 16.7 parts by weight of sodium hydroxide and 1083 parts by weight of water into a reaction bottle. After fully stirring at room temperature, 33.3 parts by weight of hydrogen peroxide was added into the reaction flask. After stirring at room temperature for 3 hours, a white precipitate was observed to separate out. Next, the resulting solution was filtered, and the filter cake was washed twice with water. Next, after drying the filter cake at 80°C, a white powder was obtained.
[0054] Next, 100 parts by weight of white powder, 106.25 parts by weight of sodium hydroxide, and 500 parts by weight of water were added into a reaction bottle. Next, after stirring at room temperature for 1 hour, the resultant was filtered, and a filter cake was collected. Next, wash the filter cake with hot pure water at 70-80° C. until the pH value of the filtrate reaches 7-8, so as to remove the residual so...
Embodiment 2
[0057] Add 6.5 parts by weight of α-cellulose (prepared by Example 1) and 100 parts by weight of N-methylmorpholine N-oxide (NMMO) in a slurry preparation tank, and increase the temperature of the slurry preparation tank to 95°C. Next, the mixture of cellulose and N-methylmorpholine N-oxide was stirred at an inner temperature of 90° C. in a slurry preparation tank under a nitrogen atmosphere. Then, after stirring for one hour, the temperature of the slurry preparation tank was raised to about 120° C., and stirred until the cellulose was completely dissolved in N-methylmorpholine N-oxide. Next, after cooling down to room temperature, the resultant was filtered, and the filtrate was collected to obtain a spinning composition (1).
Embodiment 3
[0059] 3.25 parts by weight of α-cellulose (prepared by Example 1), 3.25 parts by weight of commercially available cellulose (intrinsic viscosity is about 3.4dL / g, degree of polymerization is about 630) and 100 parts by weight of N-formazan Add morpholine N-oxide (NMMO) into a slurry preparation tank, and raise the temperature of the slurry preparation tank to 95°C. Next, the mixture of cellulose and N-methylmorpholine N-oxide was stirred at an inner temperature of 90° C. in a slurry preparation tank under a nitrogen atmosphere. Then, after stirring for one hour, the temperature of the slurry preparation tank was raised to about 120° C., and stirred until the cellulose was completely dissolved in N-methylmorpholine N-oxide. Next, after cooling down to room temperature, the resultant was filtered, and the filtrate was collected to obtain a spinning composition (2).
PUM
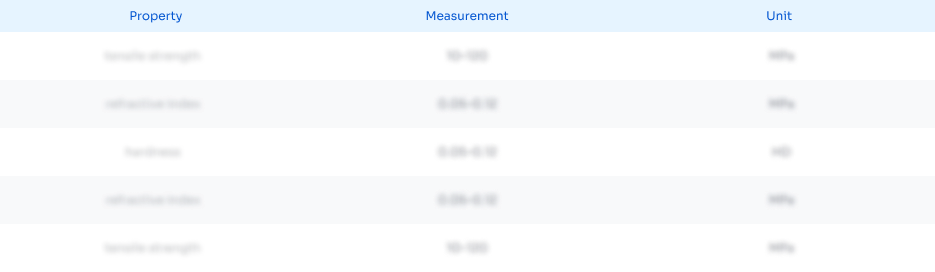
Abstract
Description
Claims
Application Information

- R&D Engineer
- R&D Manager
- IP Professional
- Industry Leading Data Capabilities
- Powerful AI technology
- Patent DNA Extraction
Browse by: Latest US Patents, China's latest patents, Technical Efficacy Thesaurus, Application Domain, Technology Topic, Popular Technical Reports.
© 2024 PatSnap. All rights reserved.Legal|Privacy policy|Modern Slavery Act Transparency Statement|Sitemap|About US| Contact US: help@patsnap.com