UV putty with high light guide performance for plate processing and preparation method of UV putty
A technology of sheet metal processing and high conductivity, applied in the field of sheet metal processing, can solve problems such as the inability to improve equipment utilization, and achieve the effects of improving initiation efficiency, reducing curing radiation dose, and good water resistance
- Summary
- Abstract
- Description
- Claims
- Application Information
AI Technical Summary
Problems solved by technology
Method used
Image
Examples
Embodiment 1
[0024] A UV putty with high light-guiding performance for plate processing, the formula of the UV putty with high light-guiding performance for plate processing is as follows: Calculated by mass percentage, 4,4'-(1-methylethylene Base) polymer of diphenol with (chloromethyl) oxirane and 2-acrylate 32%, poly α-hydrogen-ω-[(1-oxo-2-propenyl)oxy]-(oxygen- 1,2-diethyl), 2-ethyl-2-(hydroxymethyl)-1,3-propylene glycol ether (3:1) 14%, tripropylene glycol diacrylate 14%, 2,2- Polymer of bis(hydroxymethyl)-1,3-propanediol with (chloromethyl)oxirane and 2-acrylate 3%, methyl α-oxophenylacetate 2%, 1-hydroxycyclohexylbenzene 2% methyl ketone, 0.5% trimethylolpropane triacrylate, 0.8% p-hydroxyanisole, 0.8% acrylic acid, 0.9% 2-hydroxyethyl acrylate, 30% talcum powder, the talc powder The particle diameter is 800-850 mesh.
[0025] The present invention comprises the following steps when preparing the UV putty with high light-guiding performance for plate processing:
[0026] S1. Firs...
Embodiment 2
[0032]A UV putty with high light-guiding performance for plate processing, the formula of the UV putty with high light-guiding performance for plate processing is as follows: Calculated by mass percentage, 4,4'-(1-methylethylene Base) polymer of diphenol with (chloromethyl) oxirane and 2-acrylate 33%, poly α-hydrogen-ω-[(1-oxo-2-propenyl)oxy]-(oxygen- 1,2-diethyl), 2-ethyl-2-(hydroxymethyl)-1 and 3-propylene glycol ether mixture 15%, tripropylene glycol diacrylate 15%, 2,2-bis(hydroxymethyl) base)-1,3-propanediol with (chloromethyl)oxirane and 2-acrylate polymer 4%, methyl α-oxophenylacetate 3%, 1-hydroxycyclohexyl phenyl ketone 3 %, trimethylolpropane triacrylate 1%, p-hydroxyanisole 1.3%, acrylic acid 1.3%, 2-hydroxyethyl acrylate 1.4%, talcum powder 22%, and the particle diameter of the talcum powder is 800 -850 mesh.
[0033] The present invention comprises the following steps when preparing the UV putty with high light-guiding performance for plate processing:
[0034]...
Embodiment 3
[0040] A UV putty with high light-guiding performance for plate processing, the formula of the UV putty with high light-guiding performance for plate processing is as follows: Calculated by mass percentage, 4,4'-(1-methylethylene Base) polymer of diphenol with (chloromethyl) oxirane and 2-acrylate 34%, poly α-hydrogen-ω-[(1-oxo-2-propenyl)oxy]-(oxygen- 1,2-diethyl), 2-ethyl-2-(hydroxymethyl)-1,3-propylene glycol ether (3:1) 16%, tripropylene glycol diacrylate 16%, 2,2- Polymer of bis(hydroxymethyl)-1,3-propanediol with (chloromethyl)oxirane and 2-acrylate 5%, methyl α-oxophenylacetate 4%, 1-hydroxycyclohexylbenzene 4% methyl ketone, 1.5% trimethylolpropane triacrylate, 1.8% p-hydroxyanisole, 1.8% acrylic acid, 1.9% 2-hydroxyethyl acrylate, and 14% talcum powder. The particle diameter is 800-850 mesh.
[0041] The present invention comprises the following steps when preparing the UV putty with high light-guiding performance for plate processing:
[0042] S1. First put 14% of...
PUM
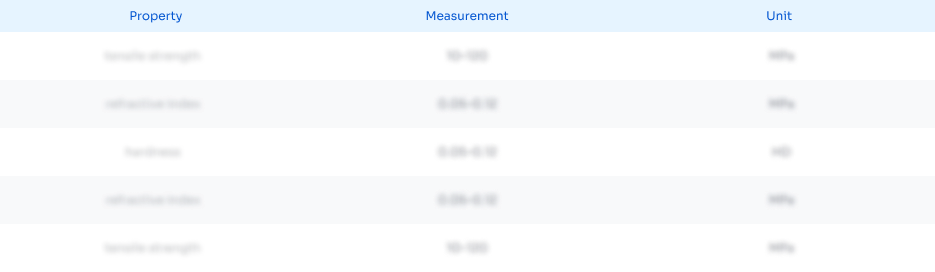
Abstract
Description
Claims
Application Information

- R&D Engineer
- R&D Manager
- IP Professional
- Industry Leading Data Capabilities
- Powerful AI technology
- Patent DNA Extraction
Browse by: Latest US Patents, China's latest patents, Technical Efficacy Thesaurus, Application Domain, Technology Topic, Popular Technical Reports.
© 2024 PatSnap. All rights reserved.Legal|Privacy policy|Modern Slavery Act Transparency Statement|Sitemap|About US| Contact US: help@patsnap.com