System and method for acidizing and roasting rare earth concentrate through multi-section external heating rotary furnace
A rare earth concentrate, acidification and roasting technology, which is applied in the system field of acidification and roasting of rare earth concentrate in a multi-stage external heat rotary furnace, can solve the problems of frequent maintenance, increased follow-up treatment of exhaust gas, and large processing gas volume, so as to reduce the difficulty of treatment and operating costs , reduce bridging and clogging, reduce the effect of sulfuric acid concentration
- Summary
- Abstract
- Description
- Claims
- Application Information
AI Technical Summary
Problems solved by technology
Method used
Image
Examples
Embodiment 1
[0041] The rare earth concentrate with a water content of 5% to 8% is transported to the rare earth silo 1, and after being measured by the metering device I2, it enters the rotary drying furnace 3. The rotary drying furnace 3 adopts flue gas jacket drying to keep the temperature of the dry material at 110 ~ Between 130°C and drying time of 0.5 hours, the dried tail gas is discharged from the gas phase outlet. The tail gas temperature is ≥120°C to prevent water vapor from condensing. After that, it is sent to the metering device II5. The dried rare earth concentrate has a water content of 0.8%, is discharged from the solid phase outlet of the rotary drying furnace 3, and then enters the metering device II5.
[0042] The dry rare earth concentrate is metered by the metering device Ⅱ5 and mixed with 100% sulfuric acid from the sulfuric acid tank 6 in a ratio of 1:1.1 in the mixing device 7, and then quickly sent to the rotary acidification furnace 8, and the heating source of th...
Embodiment 2
[0046] The rare earth concentrate with a water content of 13-15% is transported to the rare earth silo 1, and after being measured by the metering device I2, it enters the rotary drying furnace 3. The rotary drying furnace 3 uses steam tubes to dry, and the temperature of the dried material is kept at 200°C. The drying time is After 2.5 hours, the dried tail gas is discharged from the gas phase outlet. The temperature of the tail gas is ≥120°C to prevent water vapor from condensing. After the tail gas is discharged, it enters the bag filter 4. After dust removal, the tail gas reaches the standard and is discharged. After the dust is collected, it is transported to the metering device Ⅱ5 . The water content of the dried rare earth concentrate is 1%, and the dried rare earth concentrate is discharged from the rotary drying furnace 3 and enters the metering device II5.
[0047] The dry rare earth concentrate is measured by the metering device Ⅱ5 and sent to the rotary acidificati...
Embodiment 3
[0051] The rare earth concentrate with a water content of 5-10% is transported to the rare earth silo 1, and after being measured by the metering device I2, it enters the rotary drying furnace 3. The rotary drying furnace 3 adopts flue gas jacket drying to keep the temperature of the dried material at 150-180 ℃, drying time is 1 hour, the dried exhaust gas is discharged from the gas phase outlet, the exhaust gas temperature is ≥ 120 ℃, to prevent water vapor from condensing, the exhaust gas enters the bag filter 4 after being discharged, and the exhaust gas reaches the standard discharge after dust collection Transport to metering device Ⅱ5. The water content of the dried rare earth concentrate is 0.1%. The dried rare earth concentrate is discharged from the solid phase outlet of the rotary drying furnace 3 and enters the metering device II5.
[0052] The dry rare earth concentrate is metered by the metering device Ⅱ5 and mixed with 98% sulfuric acid from the sulfuric acid tan...
PUM
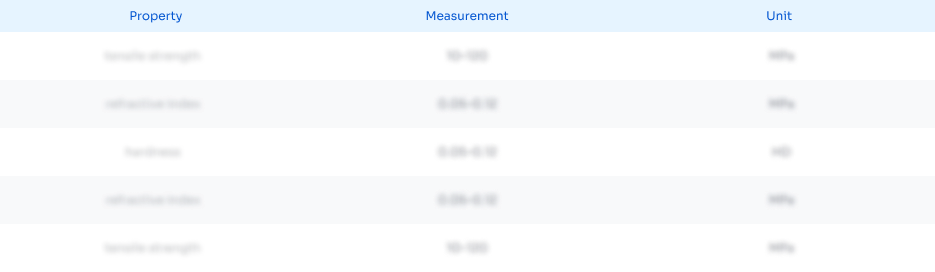
Abstract
Description
Claims
Application Information

- Generate Ideas
- Intellectual Property
- Life Sciences
- Materials
- Tech Scout
- Unparalleled Data Quality
- Higher Quality Content
- 60% Fewer Hallucinations
Browse by: Latest US Patents, China's latest patents, Technical Efficacy Thesaurus, Application Domain, Technology Topic, Popular Technical Reports.
© 2025 PatSnap. All rights reserved.Legal|Privacy policy|Modern Slavery Act Transparency Statement|Sitemap|About US| Contact US: help@patsnap.com