Multi-beam underwater steel pipe pile position measuring method
A measurement method and multi-beam technology, which are applied in the test of sheet pile walls, buildings, and foundation structures, etc., can solve the problem of submerged in seawater ten meters below the sea level, unable to carry out more accurate pile position measurement, and the detection method cannot be practical. Application and other issues, to achieve the effect of facilitating production and installation work, reducing safety risks and construction costs, and shortening construction time
- Summary
- Abstract
- Description
- Claims
- Application Information
AI Technical Summary
Problems solved by technology
Method used
Image
Examples
Embodiment Construction
[0034] The specific technical solutions of the present invention will be further described below with reference to the accompanying drawings, so that those skilled in the art can further understand the present invention, without limiting their rights.
[0035] refer to Figure 1-4 , the scheme of the present invention is used to measure the pile position parameters of underwater steel pipe piles in open sea, and the required equipment includes SONIC2024, sound velocity profiler, compass motion sensor Octans, GPS, etc.;
[0036] 1. Measuring line layout
[0037] There are two ways to arrange the survey line:
[0038] ① The measuring line is arranged in a # shape with the pile as the center, and the advantage is that the measured data is stable;
[0039] ② The measuring line is arranged in a circle with the pile as the center, which has the advantage of a large amount of data;
[0040] According to the actual situation, the optimal method is selected for measurement by compar...
PUM
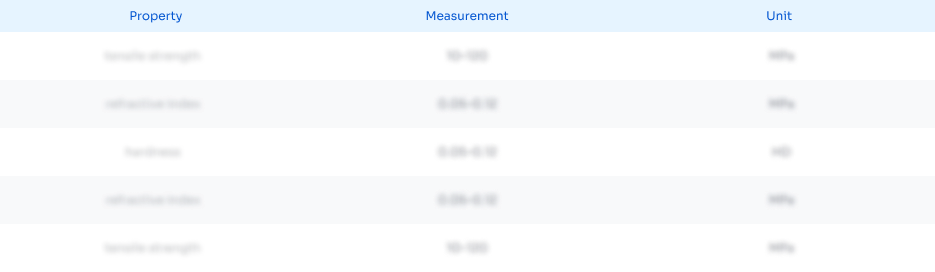
Abstract
Description
Claims
Application Information

- R&D Engineer
- R&D Manager
- IP Professional
- Industry Leading Data Capabilities
- Powerful AI technology
- Patent DNA Extraction
Browse by: Latest US Patents, China's latest patents, Technical Efficacy Thesaurus, Application Domain, Technology Topic, Popular Technical Reports.
© 2024 PatSnap. All rights reserved.Legal|Privacy policy|Modern Slavery Act Transparency Statement|Sitemap|About US| Contact US: help@patsnap.com