Preparation method for MoS2/WS2 vertical heterojunction
A heterojunction, mass ratio technology, applied in gaseous chemical plating, electrolytic coatings, surface reaction electrolytic coatings, etc., can solve the problems of easy formation of alloys, poor controllability, and low vertical heterojunction yield, etc. Ease of molybdenum-sulfur ratio, control of molybdenum-sulfur ratio, avoidance of atomic substitution and effects of thermal decomposition
- Summary
- Abstract
- Description
- Claims
- Application Information
AI Technical Summary
Problems solved by technology
Method used
Image
Examples
Embodiment 1
[0027] (1) SiO 2 Preparation of tungsten disulfide on Si substrate
[0028] with WO 3(0.05g) powder and S powder (0.2g) are the precursors, first the cut 1cm*2cm SiO 2 / Si substrates were ultrasonically cleaned in acetone and isopropanol solutions for 10 min in sequence and then cleaned with N 2 Blow dry, put a certain amount of WO 3 The powder is placed in a ceramic boat, and the SiO 2 / Si substrate is placed upside down on the ceramic boat and placed in the high temperature zone of the tube furnace, and the quartz boat with sulfur powder is placed in the low temperature zone of the tube furnace, so that the distance between the two is 36cm, and the pressure in the quartz tube is reduced by a vacuum pump. After evacuating to 0.1 Pa, the quartz tube was injected with 500 sccm of argon gas for cleaning, repeated 4 times, and the flow rate of Ar gas was set to 30 sccm after flushing. Heating the tube furnace, raising the temperature to 800°C and keeping it warm for 5 minute...
Embodiment 2
[0033] (1) SiO 2 Preparation of tungsten disulfide on Si substrate
[0034] with WO 3 (0.05g) powder and S (0.2g) powder are the precursors, first the cut 1cm*2cm SiO 2 / Si substrates were ultrasonically cleaned for 15 min in acetone and isopropanol solutions sequentially and then cleaned with N 2 Blow dry, put a certain amount of WO 3 The powder is placed in a ceramic boat, and the SiO 2 The / Si substrate is placed upside down on the ceramic boat and placed in the high temperature zone of the tube furnace, and the quartz boat filled with sulfur powder is placed in the low temperature zone of the tube furnace, so that the distance between the two is 36cm, and the pressure in the quartz tube is reduced by a vacuum pump. After evacuating to 0.1 Pa, pass 500 sccm of argon gas into the quartz tube for cleaning, repeat 5 times, and set the flow rate of Ar gas to 50 sccm after flushing. Heating the tube furnace, raising the temperature to 825°C and keeping it warm for 10 minute...
Embodiment 3
[0038] (1) SiO 2 Preparation of tungsten disulfide on Si substrate
[0039] with WO 3 (0.05g) powder and S (0.2g) powder are the precursors, first the cut 1cm*2cm SiO 2 / Si substrates were ultrasonically cleaned in acetone and isopropanol solutions for 10 min in sequence and then cleaned with N 2 Blow dry, put a certain amount of WO 3 The powder is placed in a ceramic boat, and the SiO 2 The / Si substrate is placed upside down on the ceramic boat and placed in the high temperature zone of the tube furnace, and the quartz boat filled with sulfur powder is placed in the low temperature zone of the tube furnace, so that the distance between the two is 36cm, and the pressure in the quartz tube is reduced by a vacuum pump. After evacuating to 0.1 Pa, the quartz tube was injected with 500 sccm of argon gas for cleaning, repeated 6 times, and the flow rate of Ar gas was set to 60 sccm after flushing. Heating the tube furnace, raising the temperature to 850°C and keeping it warm ...
PUM
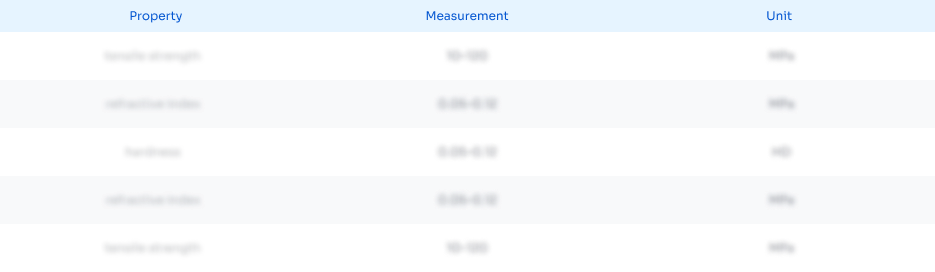
Abstract
Description
Claims
Application Information

- R&D
- Intellectual Property
- Life Sciences
- Materials
- Tech Scout
- Unparalleled Data Quality
- Higher Quality Content
- 60% Fewer Hallucinations
Browse by: Latest US Patents, China's latest patents, Technical Efficacy Thesaurus, Application Domain, Technology Topic, Popular Technical Reports.
© 2025 PatSnap. All rights reserved.Legal|Privacy policy|Modern Slavery Act Transparency Statement|Sitemap|About US| Contact US: help@patsnap.com