Method for separating salt from high-sulfur low-chlorine salt-containing wastewater
A technology of salt-containing wastewater and separation method, which is applied in alkali metal sulfite/sulfate purification, water softening, chemical instruments and methods, etc., can solve the problems of unfavorable large-scale application, uneconomical, and high process energy consumption, Achieve the effect of ensuring long-term stable operation, improving tolerance and high separation efficiency
- Summary
- Abstract
- Description
- Claims
- Application Information
AI Technical Summary
Problems solved by technology
Method used
Image
Examples
Embodiment 1
[0047] This embodiment provides a method for separating salt in high-sulfur and low-chlorine saline wastewater. The high-sulfur and low-chlorine saline wastewater to be treated is the reverse osmosis concentrated water of a refining and chemical enterprise; the process flow diagram is as follows figure 1 shown. Specific steps are as follows:
[0048] (1) pretreatment: get 15L high-sulfur and low-chlorine type saline waste water, the molar concentration ratio of sodium sulfate and sodium chloride contained in this saline waste water is 1:0.2, and total salinity is about 1.2wt%; Add 0.85g of calcium oxide and 2.65g of sodium carbonate successively in the salty wastewater to reduce the total content of calcium and magnesium to 45ppm, and then obtain the softened saline wastewater I after filtering and separating to remove the sediment; add 4.6 g to the softened saline wastewater I After adjusting the pH to 7.2 with mL concentrated hydrochloric acid, add 0.05 g of sodium hexameta...
Embodiment 2
[0067] This embodiment provides a method for separating salt in high-sulfur and low-chlorine saline wastewater. The high-sulfur and low-chlorine saline wastewater to be treated is reverse osmosis wastewater from a coal chemical enterprise; the process flow diagram is as follows figure 1 shown. Specific steps are as follows:
[0068](1) pretreatment: get 4L high-sulfur and low-chlorine type saline wastewater, the molar concentration ratio of sodium sulfate and sodium chloride contained in this saline wastewater is 1:5, and the total salinity is about 5wt%; Add 0.45g of calcium oxide and 1.6g of sodium carbonate in turn to the wastewater to reduce the total content of calcium and magnesium to 30ppm, and then filter and separate to remove the sediment to obtain softened saline wastewater I; add 1mL concentrated Adjust the pH to 8.5 with sulfuric acid and then add 0.03g of phosphine-based polyacrylic acid scale inhibitor to obtain softened saline wastewater II; 2 o 2 Removal of...
Embodiment 3
[0073] This embodiment provides a method for separating salt in high-sulfur and low-chlorine saline wastewater. The high-sulfur and low-chloride saline wastewater to be treated is high-pressure reverse osmosis concentrated water from a petrochemical enterprise; the process flow diagram is as follows figure 1 shown. Specific steps are as follows:
[0074] (1) pretreatment: get 1.5L high-sulfur low-chlorine type saline waste water, the molar concentration ratio of the sodium sulfate and sodium chloride contained in this saline waste water is 1:12, and total salinity is about 9wt%; Add 0.7g of calcium oxide and 2.2g of sodium carbonate in sequence to the salty wastewater to reduce the total content of calcium and magnesium to 42ppm, and then filter and separate to remove the precipitate to obtain softened saline wastewater I; The concentration is 10% hydrochloric acid to adjust the pH to 5.5, and then add 0.01g of amino trimethylene phosphonic acid scale inhibitor to obtain soft...
PUM
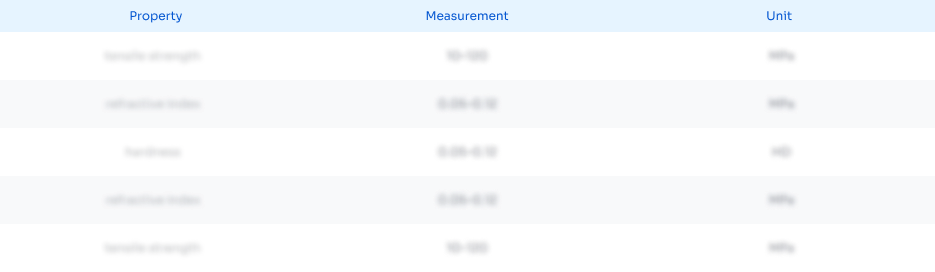
Abstract
Description
Claims
Application Information

- Generate Ideas
- Intellectual Property
- Life Sciences
- Materials
- Tech Scout
- Unparalleled Data Quality
- Higher Quality Content
- 60% Fewer Hallucinations
Browse by: Latest US Patents, China's latest patents, Technical Efficacy Thesaurus, Application Domain, Technology Topic, Popular Technical Reports.
© 2025 PatSnap. All rights reserved.Legal|Privacy policy|Modern Slavery Act Transparency Statement|Sitemap|About US| Contact US: help@patsnap.com