Preparation method of magnesium-based multifunctional composite particles
A composite particle and functional technology, applied in chemical instruments and methods, dyed low-molecular-weight organic compound treatment, fibrous fillers, etc., can solve problems such as the influence of the surface properties of flame retardants without considering the interface bonding method, and achieve the interface bonding force. Strong, improve the flame retardant efficiency, reduce the effect of adding
- Summary
- Abstract
- Description
- Claims
- Application Information
AI Technical Summary
Problems solved by technology
Method used
Image
Examples
Embodiment 1
[0029] Embodiment 1 A preparation method of magnesium-based multifunctional composite particles, comprising the following steps:
[0030] (1) Add the magnesium borate one-dimensional micro-nano material into distilled water, and ultrasonically disperse it for 15 minutes at a frequency of 20KHz to obtain a magnesium borate one-dimensional micro-nano material slurry with a mass fraction of 5%; the magnesium borate one-dimensional micro-nano material Aqueous ammonia with a mass fraction of 15% was added to the slurry to obtain slurry A.
[0031] Wherein: the ratio of the amount of ammonia water to the magnesium borate one-dimensional micro-nano material is 3.8:1.
[0032] (2) Under mechanical stirring at 600rpm / min, add magnesium chloride solution with a mass fraction of 30% to slurry A at a speed of 50g / min to obtain slurry B.
[0033] Wherein: the ratio of magnesium chloride to magnesium borate one-dimensional micro-nano material is 1.9:1.
[0034] (3) Transfer the slurry B t...
Embodiment 2
[0040] Embodiment 2 A preparation method of magnesium-based multifunctional composite particles, comprising the following steps:
[0041] (1) Add the magnesium borate one-dimensional micro-nano material into distilled water, and after ultrasonic dispersion for 30 minutes at a frequency of 50KHz, obtain a magnesium borate one-dimensional micro-nano material slurry with a mass fraction of 15%; the magnesium borate one-dimensional micro-nano material A sodium hydroxide solution with a mass fraction of 10% was added to the slurry to obtain slurry A.
[0042] Wherein: the ratio of the amount of sodium hydroxide to the magnesium borate one-dimensional micro-nano material is 15.4:1.
[0043] (2) Under mechanical stirring at 1000rpm / min, add magnesium chloride solution with a mass fraction of 10% to slurry A at a speed of 100g / min to obtain slurry B.
[0044] Wherein: the ratio of magnesium chloride to magnesium borate one-dimensional micro-nano material is 7.7:1.
[0045] (3) Trans...
Embodiment 3
[0051] Embodiment 3 A preparation method of magnesium-based multifunctional composite particles, comprising the following steps:
[0052] (1) Add the magnesium borate one-dimensional micro-nano material into distilled water, and ultrasonically disperse it for 20 minutes at a frequency of 40KHz to obtain a magnesium borate one-dimensional micro-nano material slurry with a mass fraction of 10%; the magnesium borate one-dimensional micro-nano material A potassium hydroxide solution with a mass fraction of 12% was added to the slurry to obtain slurry A.
[0053] Wherein: the ratio of the amount of potassium hydroxide to the magnesium borate one-dimensional micro-nano material is 10:1.
[0054] (2) Under mechanical stirring at 800rpm / min, add magnesium chloride solution with a mass fraction of 20% to slurry A at a speed of 80g / min to obtain slurry B.
[0055] Wherein: the ratio of magnesium chloride to magnesium borate one-dimensional micro-nano material is 5:1.
[0056] (3) Tran...
PUM
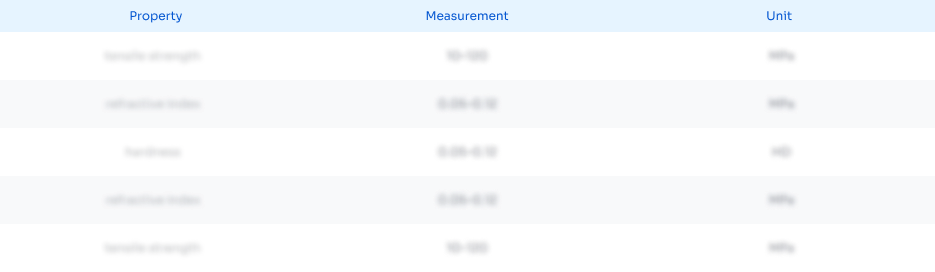
Abstract
Description
Claims
Application Information

- Generate Ideas
- Intellectual Property
- Life Sciences
- Materials
- Tech Scout
- Unparalleled Data Quality
- Higher Quality Content
- 60% Fewer Hallucinations
Browse by: Latest US Patents, China's latest patents, Technical Efficacy Thesaurus, Application Domain, Technology Topic, Popular Technical Reports.
© 2025 PatSnap. All rights reserved.Legal|Privacy policy|Modern Slavery Act Transparency Statement|Sitemap|About US| Contact US: help@patsnap.com