Preparation method for brazing aluminum alloy material and brazing aluminum alloy material
A technology of aluminum alloy materials and composite materials, which is applied in the preparation of brazed aluminum alloy materials and in the field of brazed aluminum alloy materials, can solve problems affecting brazing, energy-consuming maintenance, and production process growth, so as to save costs and avoid cleaning Equipment, the effect of shortening the production process
- Summary
- Abstract
- Description
- Claims
- Application Information
AI Technical Summary
Problems solved by technology
Method used
Image
Examples
preparation example Construction
[0030] figure 2 Shown is the flow chart of the preparation method of the above-mentioned brazed aluminum alloy material according to the embodiment of the present disclosure. The preparation method of the brazing aluminum alloy material comprises the steps of material compounding, hot rolling, intermediate rolling, intermediate annealing, final rolling, stretch bending and straightening. specifically:
[0031] Material Composite: Press figure 1 As shown, the core material and the skin material are combined to obtain a composite material.
[0032] Hot rolling: preheating the composite material, and hot rolling the preheated composite material to a thickness of 5-10 mm to obtain a hot-rolled strip. Optionally, during hot rolling, the composite material is preheated at a temperature of 450° C. to 550° C., and the holding time is 2 to 10 hours.
[0033] Intermediate rolling: The hot-rolled strip is subjected to intermediate cold rolling to obtain cold-rolled strip foil. Opti...
Embodiment 1
[0042] The brazing aluminum alloy material provided in this embodiment is formed by rolling a core material and a skin material. Among them, the core material is 3003MOD, including: Si: 0.6wt%, Fe: 0.7wt%, Cu: 0.05~0.2wt%, Mn: 1.0~1.5wt%, Zn: 0.1wt%, the rest is Al and less than 0.15wt% % of unavoidable impurities.
[0043] The leather material is 4045, including: Si: 9~11wt%, Fe: 0.8wt%, Cu: 0.3wt%, Mn: 0.05wt%, Zn: 0.1wt%, Ti: 0.2wt%, Mg: 0.05wt%, The remainder is Al and less than 0.15 wt% of unavoidable impurities. The composite ratio of leather materials on both sides is 5%;
[0044] The preparation process of the above-mentioned brazing aluminum alloy material is as follows:
[0045] 3003MOD and 4045 aluminum alloys were put into melting furnaces for melting respectively, and 3003MOD and 4045 ingots were prepared by semi-continuous casting method. 4045 is preheated, the preheating temperature is 450°C, the holding time is 10h, and then hot rolling is carried out.
[...
Embodiment 2
[0048] The brazing aluminum alloy material provided in this embodiment is formed by rolling a core material and a skin material. Among them, the core material is 3003MOD, including: Si: 0.6wt%, Fe: 0.7wt%, Cu: 0.05~0.2wt%, Mn: 1.0~1.5wt%, Zn: 0.1wt%, the rest is Al and less than 0.15wt% % of unavoidable impurities.
[0049] The leather material is 4045, including: Si: 9~11wt%, Fe: 0.8wt%, Cu: 0.3wt%, Mn: 0.05wt%, Zn: 0.1wt%, Ti: 0.2wt%, Mg: 0.05wt%, The remainder is Al and less than 0.15 wt% of unavoidable impurities. The composite ratio of leather materials on both sides is 15%;
[0050] The preparation process of the above-mentioned brazing aluminum alloy material is as follows:
[0051] 3003MOD and 4045 aluminum alloys were put into melting furnaces for melting respectively, and 3003MOD and 4045 ingots were prepared by semi-continuous casting method. 4045 is preheated, the preheating temperature is 500°C, the holding time is 6h, and then hot rolling is carried out.
[...
PUM
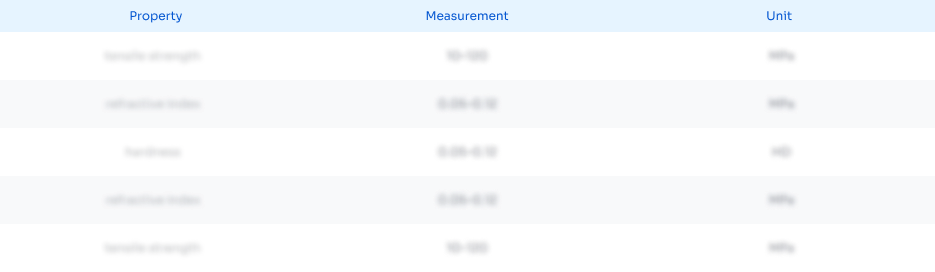
Abstract
Description
Claims
Application Information

- Generate Ideas
- Intellectual Property
- Life Sciences
- Materials
- Tech Scout
- Unparalleled Data Quality
- Higher Quality Content
- 60% Fewer Hallucinations
Browse by: Latest US Patents, China's latest patents, Technical Efficacy Thesaurus, Application Domain, Technology Topic, Popular Technical Reports.
© 2025 PatSnap. All rights reserved.Legal|Privacy policy|Modern Slavery Act Transparency Statement|Sitemap|About US| Contact US: help@patsnap.com