High-whiteness yellowing-resistant coated ivory board and preparation method thereof
A technology of cloth white cardboard and high whiteness, which is applied in the field of high whiteness anti-yellowing coated white cardboard and its preparation, which can solve the problems of low paper strength, unnaturalness, dazzling paper hue and visual sense, etc., and achieve improvement Resistance to yellowing and the effect of reducing paper odor
- Summary
- Abstract
- Description
- Claims
- Application Information
AI Technical Summary
Problems solved by technology
Method used
Image
Examples
preparation example Construction
[0041] The invention provides a preparation method of high-whiteness coated yellow-returning-resistant white cardboard, comprising: S1) pulp treatment: after bleaching kraft hardwood pulp is mixed with a first biological enzyme for treatment, after pulping treatment, Obtain broad-leaf fiber pulp; mix bleached kraft softwood pulp with a second biological enzyme for treatment, and then undergo pulping treatment to obtain soft-leaf fiber pulp; or bleach kraft broad-leaf pulp and bleached kraft softwood pulp After the mixed wood pulp is mixed with the second biological enzyme for treatment, it is refined to obtain mixed fiber pulp; the first biological enzyme and the second biological enzyme are each independently selected from cellulase and / or hemicellulase ; S2) slurry mixing: mixing one or more of the broadleaf fiber slurry, coniferous fiber slurry and mixed fiber slurry to obtain surface layer slurry; One or more of the slurry and the mixed fiber slurry are mixed with the fluo...
Embodiment 1
[0065] according to figure 2 The manufacturing process shown includes the following steps:
[0066] 1) Fiber treatment
[0067] Bleached kraft hardwood pulp 1: Dilute and disintegrate the air-dried bleached kraft hardwood pulp board at a concentration of 5% in the pulper 1, and add 1.5kg / ton of kraft pulp to the pre-grinding tank 1 in terms of dry pulp. Dry pulp cellulase, after the slurry is treated with biological enzymes in the pre-grinding pool 1 for 100 minutes, the concentration is adjusted to a refining concentration of 4.25%, and sent to the disc mill 1 refining machine for refining treatment, and the freeness after refining is controlled to 539ml. Get Fiber 1.
[0068] Bleached kraft hardwood pulp 2: Dilute and disintegrate the air-dried bleached kraft hardwood pulp board in the pulper 2 at a concentration of 5%. Dry pulp cellulase, after the slurry is treated with biological enzymes in the pre-grinding pool 2 for 110 minutes, the concentration is adjusted to a re...
Embodiment 2
[0086] according to image 3 The manufacturing process shown includes the following steps:
[0087] 1) Fiber treatment
[0088] Bleached kraft hardwood pulp 1: Dilute and disintegrate the air-dried bleached kraft hardwood pulp board at a concentration of 5% in the pulper 1, and add 1.5kg / ton of kraft pulp to the pre-grinding tank 1 in terms of dry pulp. Dry pulp cellulase, after the slurry is treated with biological enzymes in the pre-grinding pool 1 for 100 minutes, the concentration is adjusted to a refining concentration of 4.14%, and sent to the disc mill 1 refining machine for refining treatment, and the freeness after refining is controlled to 531ml. Get Fiber 1.
[0089] Bleached kraft hardwood pulp 2: Dilute and disintegrate the air-dried bleached kraft hardwood pulp board in the pulper 2 at a concentration of 5%. Dry pulp cellulase, after the slurry is treated with biological enzymes in the pre-grinding pool 2 for 110 minutes, the concentration is adjusted to a ref...
PUM
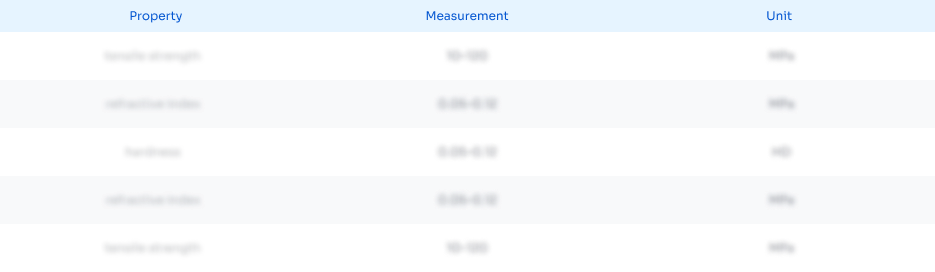
Abstract
Description
Claims
Application Information

- R&D
- Intellectual Property
- Life Sciences
- Materials
- Tech Scout
- Unparalleled Data Quality
- Higher Quality Content
- 60% Fewer Hallucinations
Browse by: Latest US Patents, China's latest patents, Technical Efficacy Thesaurus, Application Domain, Technology Topic, Popular Technical Reports.
© 2025 PatSnap. All rights reserved.Legal|Privacy policy|Modern Slavery Act Transparency Statement|Sitemap|About US| Contact US: help@patsnap.com