Preparation method of modified starch adhesive
A starch adhesive and modification technology, which is applied in the direction of starch-derived adhesives, adhesive additives, adhesive types, etc., can solve the problems of combustion emissions polluting the environment, workshop temperature rise, and high gelatinization temperature. Achieve the effects of avoiding too strong alkalinity, increasing mass transfer rate, and improving water resistance
- Summary
- Abstract
- Description
- Claims
- Application Information
AI Technical Summary
Problems solved by technology
Method used
Image
Examples
Embodiment 1
[0030] Step 1: In the spray loop reactor (1) using Venturi nozzle, add 400 parts of water, 100 parts of tapioca starch, 100 parts of 10% polyvinyl alcohol solution, 2 parts of Sodium tripolyphosphate, 8 parts of hydrogen peroxide, 0.5 part of ferrous sulfate powder, open described external circulation pump (5) and carry out high-speed jet mixing;
[0031] Step 2: Control the temperature at 20°C, slowly add 10 parts of 20 parts of monochloromethane gas and sodium hydroxide solution to the injection loop through the second feed port (3) and the first feed port (4) respectively In the reactor, the jet reactor is sprayed and mixed to realize a sufficient reaction between the materials, and the feeding time is 2 hours. After the feeding is completed, the reaction is completed after the jet loop reactor continues to react for 2 hours.
Embodiment 2
[0033] Step 1: In the spray loop reactor (1) using Venturi nozzle, add 350 parts of water, 100 parts of potato starch, 80 parts of 8% polyvinyl alcohol solution, 1.6 parts in the first feed port (4) successively Ferric chloride, 5 parts of hydrogen peroxide, 0.5 part of ferrous sulfate powder, open the external circulation pump (5) and carry out high-speed jet mixing.
[0034] Step 2: Control the temperature at 40°C, slowly add 8 parts of monochloromethane gas and 15 parts of sodium hydroxide solution to the injection loop through the second feed port (3) and the first feed port (4) respectively In the reactor, the jet reactor is sprayed and mixed to realize a sufficient reaction between the materials, and the feeding time is 2 hours. After the feeding is completed, after the jet loop reactor continues to react for 1 hour, the reaction ends;
Embodiment 3
[0036] Step 1: In the injection loop reactor (1) using Venturi nozzle, add 400 parts of water, 100 parts of cornstarch, 80 parts of 8% polyvinyl alcohol solution, 1 part of Alum, 5 parts of hydrogen peroxide, 0.5 part of ferrous sulfate powder, open the external circulation pump (5) and carry out high-speed jet mixing.
[0037] Step 2: Control the temperature at 40°C, slowly add 8 parts of monochloromethane gas and 16 parts of sodium hydroxide solution to the injection loop through the second feed port (3) and the first feed port (4) respectively In the reactor, the jet reactor is sprayed and mixed to realize a sufficient reaction between the materials, and the feeding time is 2 hours. After the feeding is completed, after the jet loop reactor continues to react for 1 hour, the reaction ends;
PUM
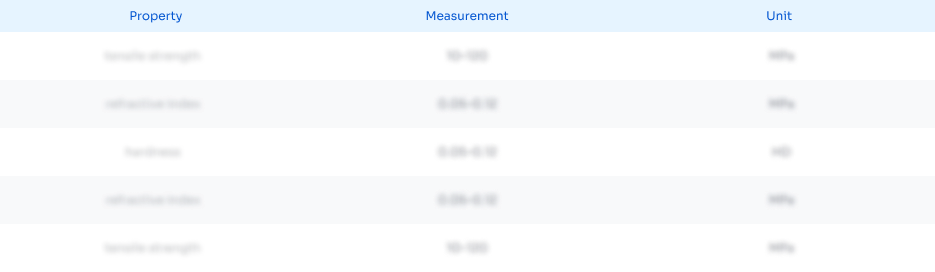
Abstract
Description
Claims
Application Information

- R&D
- Intellectual Property
- Life Sciences
- Materials
- Tech Scout
- Unparalleled Data Quality
- Higher Quality Content
- 60% Fewer Hallucinations
Browse by: Latest US Patents, China's latest patents, Technical Efficacy Thesaurus, Application Domain, Technology Topic, Popular Technical Reports.
© 2025 PatSnap. All rights reserved.Legal|Privacy policy|Modern Slavery Act Transparency Statement|Sitemap|About US| Contact US: help@patsnap.com