Complex-shape large thin-wall part and manufacturing process thereof
A technology for large thin-walled parts and complex shapes, applied in the direction of slender components, building components, etc., can solve the problems of forging difficulties, length deviation, difficult to grasp the accuracy, etc., to achieve high product dimensional accuracy, reduce production time, and save manufacturing cost effect
- Summary
- Abstract
- Description
- Claims
- Application Information
AI Technical Summary
Problems solved by technology
Method used
Image
Examples
Embodiment Construction
[0021] The present invention will be further described below in conjunction with accompanying drawing:
[0022] Such as figure 1 As shown, a large thin-walled part with a complex shape comprises a thin-walled part body 2, one end of the thin-walled part body 2 is provided with a head 1, the other end of the thin-walled part body 2 is provided with a tail part 4, and the inside of the thin-walled part body 2 is provided with There are cavities 3 . The thickness of the head 1 is greater than that of the tail 4 . The diameter of the head 1 is smaller than that of the tail 4 .
[0023] A manufacturing process for large thin-walled parts with complex shapes, the manufacturing process includes the following steps: (1) Screening and selecting hollow tubes that meet requirements. (2) Cutting the material, intercepting the hollow tube of fixed length according to the requirements. (3) Heat treatment, put the hollow tube into a heating furnace for heating, the heating temperature is...
PUM
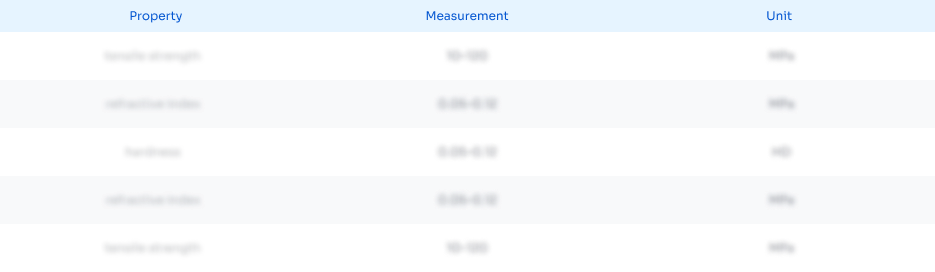
Abstract
Description
Claims
Application Information

- R&D Engineer
- R&D Manager
- IP Professional
- Industry Leading Data Capabilities
- Powerful AI technology
- Patent DNA Extraction
Browse by: Latest US Patents, China's latest patents, Technical Efficacy Thesaurus, Application Domain, Technology Topic, Popular Technical Reports.
© 2024 PatSnap. All rights reserved.Legal|Privacy policy|Modern Slavery Act Transparency Statement|Sitemap|About US| Contact US: help@patsnap.com