A kind of production process of turning needle
A production process and transfer piece technology, applied in knitting, weft knitting, textiles and papermaking, etc., can solve the problems of shortening the service life of knitting needles, improving the production cost of enterprises, reducing the qualified rate of products, etc., and achieving toughness And the appearance quality is improved, the service life is extended, and the wear-resistant service life is long.
- Summary
- Abstract
- Description
- Claims
- Application Information
AI Technical Summary
Problems solved by technology
Method used
Image
Examples
Embodiment Construction
[0021] Specific embodiments of the present invention will be described in detail below in conjunction with the accompanying drawings.
[0022] Transfer piece production process:
[0023] 1) Blank preparatory heat treatment: Cut the strip-shaped T10 blank into strip-shaped blanks of 1000mm each, and then fasten and fix the strip-shaped blanks in groups of 5 with special clamps, and put them into an electric furnace for preliminary heat treatment. The preparatory heat treatment is normalizing treatment, the normalizing treatment temperature is kept at 770-790°C, and the temperature is kept for 12-15 minutes; then the blank is subjected to high-temperature tempering, the high-temperature tempering temperature is 550-650°C, and the temperature is kept for 3-5 minutes, and then Cooling to room temperature in still air, the purpose is to eliminate the stress generated during normalizing cooling and improve toughness and plasticity.
[0024] 2) Flatten the pre-heat-treated blank, pl...
PUM
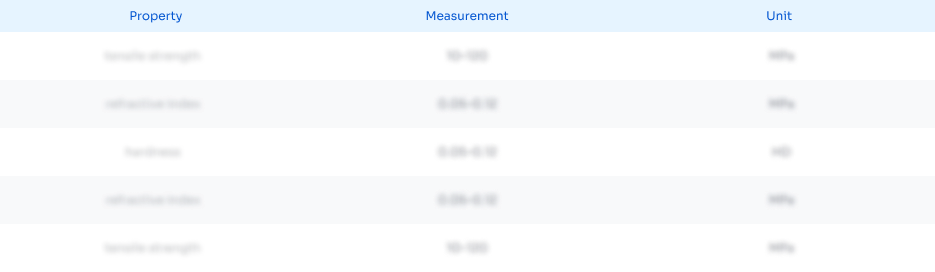
Abstract
Description
Claims
Application Information

- R&D
- Intellectual Property
- Life Sciences
- Materials
- Tech Scout
- Unparalleled Data Quality
- Higher Quality Content
- 60% Fewer Hallucinations
Browse by: Latest US Patents, China's latest patents, Technical Efficacy Thesaurus, Application Domain, Technology Topic, Popular Technical Reports.
© 2025 PatSnap. All rights reserved.Legal|Privacy policy|Modern Slavery Act Transparency Statement|Sitemap|About US| Contact US: help@patsnap.com