Method for separating and extracting vanadium and nickel from waste catalysts
A waste catalyst, vanadium-nickel technology, applied in the field of separation and extraction of valuable metals from solid waste resources, can solve the problems of vanadium recovery rate of only 72-78.3%, high processing temperature, low vanadium recovery rate, etc. Low temperature, avoiding the effect of simultaneous leaching
- Summary
- Abstract
- Description
- Claims
- Application Information
AI Technical Summary
Problems solved by technology
Method used
Examples
Embodiment 1
[0077] Get nickel-containing 0.52%Ni, 0.3%V waste ultra-stable Y-type FCC catalyst 1000g, add 100g graphite, 50g calcium chloride and 100g vanadium-nickel collector (mol ratio is 1:1 iron powder and Composed of ferric oxide) mixed and ground to 200 mesh, then added 150g of water to make pellets with a diameter of 1cm, and then roasted at 1050°C (into nitrogen during the process) for 60min, and then continued to increase the temperature to 1200°C at Roasting (into nitrogen during the process) 90min. After roasting, the material is ground to 150 meshes, and then separated by magnetic separation to obtain a sponge iron alloy enriched in nickel and vanadium. The recovery rate of nickel was 93.2%, and the recovery rate of vanadium was 90.1%.
Embodiment 2
[0094] Get nickel-containing 5%Ni, 1000g of ultra-stable Y-type FCC spent catalyst of 1.5%V, add 400g coke, 300g calcium chloride and 200g vanadium-nickel collector (the mol ratio is 1.5:1 iron powder and ferric oxide Composition) Mix and grind to 150 mesh, add 100g of water to make pellets with a diameter of 3cm, then roast at 950°C for 120min, continue to raise the temperature to 1250°C for roasting (in the process, N 2 ) for 30 minutes, after roasting, the material was ground to 200 mesh, and then separated by magnetic separation to obtain sponge iron alloy A enriched in nickel and vanadium. The recovery rate of nickel was 99.2%, and the recovery rate of vanadium was 96.6%.
[0095]Sponge iron alloy A was oxidized and roasted at 500°C for 40 minutes, and then according to the theoretical amount of sodium metavanadate generated by the reaction of vanadium and sodium carbonate in sponge iron alloy A, sodium carbonate was added to the roasted material and mixed by ball milling...
Embodiment 3
[0106] Get nickel-containing 0.2%Ni, 2000g of the ultra-stable Y-type spent FCC catalyst of 0.1%V, add 400g petroleum coke, 100g calcium chloride and 300g vanadium-nickel collector (leaching in iron powder and embodiment 2) in spent catalyst Slag C; the molar ratio is 1:1) mixed and ground to 80 mesh, then added 300g of water to make pellets with a diameter of 2cm, and then roasted at 1000°C (introducing N2 during the process) for 90min, and continued to increase the temperature to Baking at 1210°C (in the process of feeding N2) for 50min. After roasting, the material is ground to 180 mesh and separated by magnetic separation to obtain sponge iron alloy A1 enriched in nickel and vanadium. The recovery rate of nickel was 92.4%, and the recovery rate of vanadium was 90.8%.
[0107] Sponge iron alloy A1 was oxidized and roasted at 400°C for 120 minutes, then 1.5 times the theoretical amount of sodium metavanadate produced by the reaction of vanadium and sodium bicarbonate in spo...
PUM
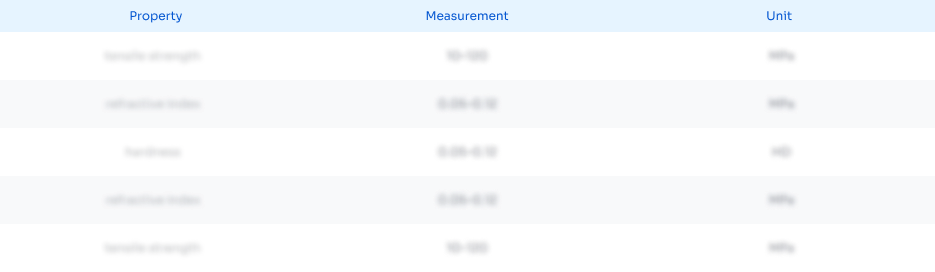
Abstract
Description
Claims
Application Information

- R&D
- Intellectual Property
- Life Sciences
- Materials
- Tech Scout
- Unparalleled Data Quality
- Higher Quality Content
- 60% Fewer Hallucinations
Browse by: Latest US Patents, China's latest patents, Technical Efficacy Thesaurus, Application Domain, Technology Topic, Popular Technical Reports.
© 2025 PatSnap. All rights reserved.Legal|Privacy policy|Modern Slavery Act Transparency Statement|Sitemap|About US| Contact US: help@patsnap.com