Early strength agent for pavement concrete
A technology of concrete and early strength agent, which is applied in the field of concrete admixture, which can solve the problems of system strength decrease, low-temperature strength of concrete, and structural body damage, etc., to achieve enhanced solid phase body volume expansion, enhanced early cement strength, and accelerated wetting and penetration effects
- Summary
- Abstract
- Description
- Claims
- Application Information
AI Technical Summary
Problems solved by technology
Method used
Image
Examples
Embodiment 1
[0036] combine figure 1 , an early strength agent for pavement concrete, based on concrete benchmark cement, including the following raw materials in parts by weight: 1.8 parts of sodium sulfate, 2 parts of gypsum, 0.05 parts of triethanolamine, and 1 part of sodium chloride.
[0037] The benchmark cement that described concrete adopts is Hubo brand slag portland cement 32.5 grades, and the standard consistency water consumption of described benchmark cement is 140.0g, and the initial setting time of described benchmark cement is 283min, and the final setting time of described benchmark cement 368min, the sodium sulfate adopts industrial grade sodium sulfate, and the purity of the sodium sulfate is more than or equal to 95%.
[0038] Triethanolamine has an emulsifying effect. After adding triethanolamine to the cement slurry, the triethanolamine molecules are adsorbed on the surface of cement particles to form a charged hydrophilic film, which reduces the surface tension of th...
Embodiment 2
[0041] The performance detection of described accelerator comprises the steps:
[0042] 1) Measure and weigh according to the proportioning design of each component raw material, and set aside;
[0043] 2) Put 1.8 parts of sodium sulfate, 2 parts of gypsum, 0.05 parts of triethanolamine and 1 part of sodium chloride weighed in step 1) into the reaction kettle and stir at 40-50 r / min, add an appropriate amount of water, mix and stir until Dissolve completely to obtain early strength agent;
[0044] 3) Stir 100 parts of cement, 400-450 parts of sand, 2-5 parts of early strength agent and 1-3 parts of water reducer in the mixer for 45-60 minutes according to the ratio of parts by mass, and the stirring speed is 40-50r / min, so that the early strength agent is evenly mixed with cement and sand to get mixed soil;
[0045] 4) Add 5-10 parts of mixing water to 100 parts of mixing soil according to the ratio of parts by mass, stir the mixing soil at 40-50r / min for 40-60min to obtain...
Embodiment 3
[0047] On the basis of Example 2, the fluidity loss rate of the cement slurry is: S=(F1-F2) / F1×100, where S represents the fluidity loss rate (%), and F1 represents the flow of the cement slurry at 0 min degree (cm), F2 means the fluidity (cm) of cement slurry at 30 minutes, the mix ratio used in the mortar test is: cement (C): sand (S) = 1: 2.25, water-cement ratio (W / C )=0.36.
[0048] The drying shrinkage test of the mortar includes the following steps: directly measure the length of the 40mm×40mm×160mm test block with a mortar ratio meter, and measure the ages of 3d, 5d, 7d, 14d, 21d, and 28d respectively with the initial length L0 of 1d. The length of the test block, the curing condition is 50% relative humidity, 20 ℃, and the drying shrinkage rate of the test block of the corresponding age is calculated.
[0049] Further, the drying shrinkage S of the mortar t Meet: S t =(L 0 -L t )×100 / l, where, S t Indicates the dry shrinkage rate of cement mortar when the age is...
PUM
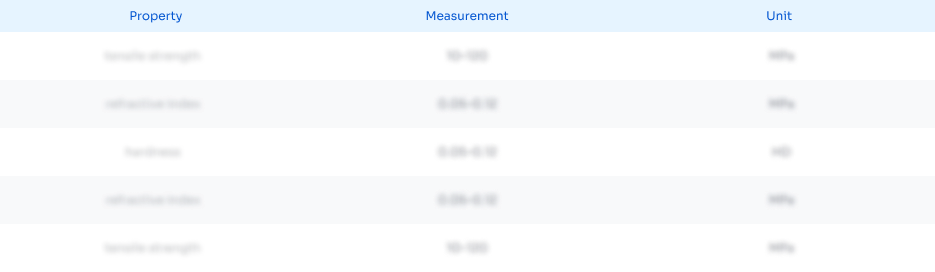
Abstract
Description
Claims
Application Information

- R&D
- Intellectual Property
- Life Sciences
- Materials
- Tech Scout
- Unparalleled Data Quality
- Higher Quality Content
- 60% Fewer Hallucinations
Browse by: Latest US Patents, China's latest patents, Technical Efficacy Thesaurus, Application Domain, Technology Topic, Popular Technical Reports.
© 2025 PatSnap. All rights reserved.Legal|Privacy policy|Modern Slavery Act Transparency Statement|Sitemap|About US| Contact US: help@patsnap.com