Positive and negative sample data balancing method in factory PCB defect detection
A PCB board and defect detection technology, applied in the field of data processing, can solve problems such as model overfitting, positive and negative sample imbalance, etc., and achieve the effect of strong robustness, broad market application prospects, and superior synthesis effect
- Summary
- Abstract
- Description
- Claims
- Application Information
AI Technical Summary
Problems solved by technology
Method used
Image
Examples
Embodiment 1
[0053] Such as Figure 1 to Figure 5 As shown, the present embodiment discloses a positive and negative sample data balance method in a factory PCB board defect detection, and the balance method mainly includes the following specific steps:
[0054] 1) Collect, organize and classify data sets: collect image data sets of factory PCB boards, organize the data sets, and manually classify according to whether there are defects.
[0055] Specifically, in step 1) data preprocessing needs to set specific and clear classification rules, and the classification boundaries cannot be blurred. A positive sample refers to a PCB without defects, and a negative sample refers to a defective PCB.
[0056] Preferably, for simplicity, the input images are all regularized to a size of 256*256.
[0057] 2) Construct a generative adversarial network model to solve the problem of imbalance between positive and negative samples, aiming to design a network structure based on two groups of unidirectio...
Embodiment 2
[0077] combine Figure 1 to Figure 8 As shown, this embodiment discloses a method for balancing positive and negative sample data in a factory PCB board defect detection, including the following specific implementation steps:
[0078] 1) Collect the image data set of the PCB board in the factory, organize the data set, and manually classify it according to whether there are defects.
[0079] 2) Construct a generative adversarial network model to solve the problem of imbalance between positive and negative samples. The envisaged method is unsupervised image-to-image translation, aiming to design a network structure based on two sets of unidirectional GANs and achieve bidirectional image generation.
[0080] 3) The model is divided into generator and discriminator. Firstly, the generator module is designed. Generators include encoders, converters and decoders.
[0081] 4) Design of the encoder. Different channels of the encoder output feature map combine different features ...
PUM
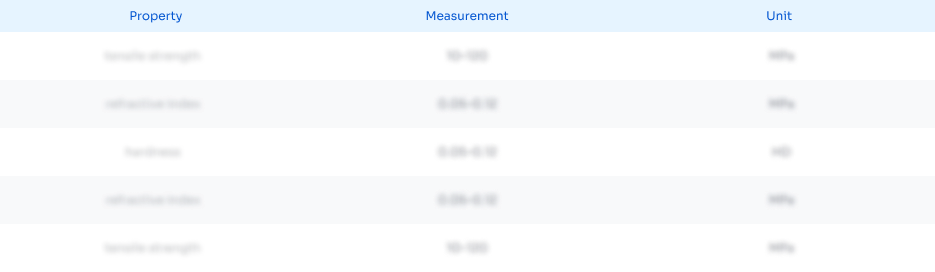
Abstract
Description
Claims
Application Information

- R&D Engineer
- R&D Manager
- IP Professional
- Industry Leading Data Capabilities
- Powerful AI technology
- Patent DNA Extraction
Browse by: Latest US Patents, China's latest patents, Technical Efficacy Thesaurus, Application Domain, Technology Topic, Popular Technical Reports.
© 2024 PatSnap. All rights reserved.Legal|Privacy policy|Modern Slavery Act Transparency Statement|Sitemap|About US| Contact US: help@patsnap.com