Polyester spinning oil agent
A spinning oil and polyester technology, applied in the field of polyester spinning oil, can solve the problems of oil mist pollution, easy volatilization of chemical fiber oil, etc., and achieve the effects of convenient control, good anti-oxidative stability and good compatibility
- Summary
- Abstract
- Description
- Claims
- Application Information
AI Technical Summary
Problems solved by technology
Method used
Examples
Embodiment 1
[0019] The present embodiment determines that the ratio of each component is by weight percentage;
[0020] 92.5 parts of naphthenic mineral oil,
[0021] 4 parts of fatty alcohol polyoxyethylene ether,
[0022] 1.5 parts of polyisobutylene,
[0023] 0.5 parts of isotridecanyl phosphate,
[0024] 1.5 parts of polyethylene glycol monooleate.
[0025] After batching according to the above ratio, pump naphthenic mineral oil, fatty alcohol polyoxyethylene ether, polyisobutylene, and isotridecanyl phosphate into the reaction kettle, start stirring, raise the temperature to about 50°C, stir evenly, and then keep the temperature at 50°C Stir for 30 minutes at about ℃, finally add polyethylene glycol monooleate, stir for 15 minutes, after the stirring is completed, cool to about 40℃, discharge, filter and pack.
Embodiment 2
[0027] The present embodiment determines that the ratio of each component is by weight percentage;
[0028] 90.5 parts of naphthenic mineral oil,
[0029] 4.5 parts of fatty alcohol polyoxyethylene ether,
[0030] 1.5 parts of polyisobutylene,
[0031] 1 part of isotridecanyl phosphate,
[0032] 2.5 parts of polyethylene glycol monooleate;
[0033] After batching according to the above ratio, pump naphthenic mineral oil, fatty alcohol polyoxyethylene ether, polyisobutylene, and isotridecanyl phosphate into the reaction kettle, start stirring, raise the temperature to about 50°C, stir evenly, and then keep the temperature at 80°C Stir for 30 minutes at about ℃, finally add polyethylene glycol monooleate, stir for 15 minutes, after the stirring is completed, cool to about 40℃, discharge, filter, and pack.
Embodiment 3
[0035] The present embodiment determines that the ratio of each component is by weight percentage;
[0036] 89.5 parts of naphthenic mineral oil,
[0037] 5 parts of fatty alcohol polyoxyethylene ether,
[0038] 2.5 parts of polyisobutylene,
[0039] 1 part of isotridecanyl phosphate,
[0040] 2 parts of polyethylene glycol monooleate;
[0041] After batching according to the above ratio, pump naphthenic mineral oil, fatty alcohol polyoxyethylene ether, polyisobutylene, and isotridecanyl phosphate into the reaction kettle, start stirring, raise the temperature to about 50°C, stir evenly, and then keep the temperature at 80°C Stir for 40 minutes at about ℃, finally add polyethylene glycol monooleate, stir for 15 minutes, after the stirring is completed, cool to about 40℃, discharge, filter, and pack.
PUM
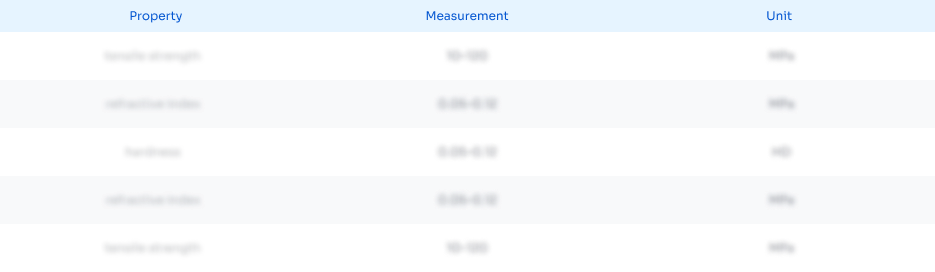
Abstract
Description
Claims
Application Information

- Generate Ideas
- Intellectual Property
- Life Sciences
- Materials
- Tech Scout
- Unparalleled Data Quality
- Higher Quality Content
- 60% Fewer Hallucinations
Browse by: Latest US Patents, China's latest patents, Technical Efficacy Thesaurus, Application Domain, Technology Topic, Popular Technical Reports.
© 2025 PatSnap. All rights reserved.Legal|Privacy policy|Modern Slavery Act Transparency Statement|Sitemap|About US| Contact US: help@patsnap.com