A Welding Method for Thick Plate Penetration Welding H-Shaped Steel without Carbon Gouging
A technology of penetration welding and welding method, applied in welding/welding/cutting items, welding equipment, arc welding equipment, etc., can solve the problems of complex processing, long cycle, high cost, improve weld quality and slow production speed , the effect of saving the cost of consumables
- Summary
- Abstract
- Description
- Claims
- Application Information
AI Technical Summary
Problems solved by technology
Method used
Image
Examples
Embodiment Construction
[0032] The present invention will be further described below in conjunction with the accompanying drawings and embodiments.
[0033] Such as Figure 1-7 shown.
[0034] A welding method for thick plate penetration welding H-shaped steel without carbon planing. Take one side as an example, and the other side needs to be turned over for reference. It includes the following steps:
[0035] (1) H-shaped steel web and flange blanking. Gas cutting is used for blanking, and the cutting surface should be free of cracks, slag inclusions, and delamination. A 4mm welding gap is left on one side of the web blanking, and the blanking width is reduced by 8mm from the web width;
[0036] (2) Open the bevel. The beveling machine is used to open the beveling machine. The front bevel depth is 15mm, the bevel angle is 35 degrees, the back bevel depth is 11mm, the bevel angle is 40 degrees, and the root is 2mm in the middle, such as figure 2 shown;
[0037] (3) H-beam assembly. Before asse...
PUM
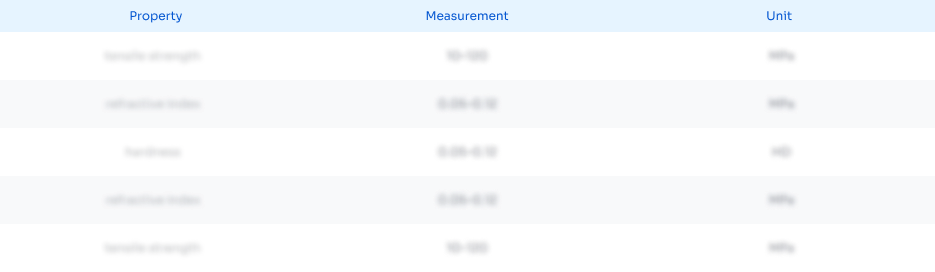
Abstract
Description
Claims
Application Information

- R&D Engineer
- R&D Manager
- IP Professional
- Industry Leading Data Capabilities
- Powerful AI technology
- Patent DNA Extraction
Browse by: Latest US Patents, China's latest patents, Technical Efficacy Thesaurus, Application Domain, Technology Topic, Popular Technical Reports.
© 2024 PatSnap. All rights reserved.Legal|Privacy policy|Modern Slavery Act Transparency Statement|Sitemap|About US| Contact US: help@patsnap.com